Pipe class outlines a set of compatible piping components (like pipes, fittings, and valves) based on design and service criteria, ensuring system compatibility and adherence to required conditions. It includes material types, pressure ratings, and corrosion allowances. Pipe specification, however, details technical requirements for pipe manufacturing alone, covering dimensions, material grades, and testing based on standards for specific projects.
The difference lies in scope: pipe class ensures component compatibility within a system, while pipe specification focuses on pipe manufacturing standards. Together, they ensure piping system safety, efficiency, and standard compliance.
PIPE CLASS & PIPE SPECIFICATION
In the domains of piping engineering and design, particularly within the oil & gas industry, construction industry, and power generation industry, the terms “pipe class” and “pipe specification” play pivotal roles. Understanding these concepts is essential for ensuring the safe, efficient, and cost-effective transportation of fluids. This detailed exploration will clarify what these terms mean and highlight the distinctions between them.
WHAT IS A PIPE CLASS?
The term “pipe class” refers to a categorization system used to define a set of piping components that share common design and construction criteria. A pipe class is typically established by an organization (for example an EPC Contractor like Petrofac or an End-User like British Petroleum) to standardize the types of pipes, fittings, valves, and other components used in their piping systems based on specific operating conditions. These conditions include the fluid service, pressure-temperature ratings, and corrosion allowances, among others.
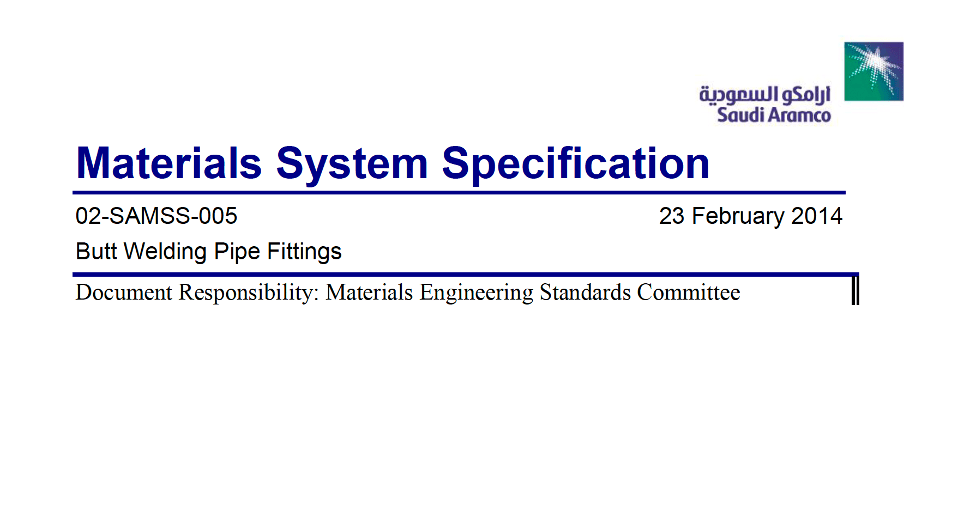
A pipe class is essentially a template that dictates the materials, thickness, and types of components that can be used for particular applications or for a specific project. It is designed to ensure that all components within a class are compatible with each other and suitable for the specified service conditions. For example, a pipe class for high-pressure steam service would specify materials that can withstand high temperatures and pressures, along with appropriate corrosion allowances.
INFORMATION IN PIPE CLASSES
Pipe classes typically contain a comprehensive set of information that standardizes the design and components of piping systems for specific operational conditions. The information provided in a pipe class ensures that all components within a class are compatible with each other and suitable for their intended application. Here’s what is usually included in pipe classes:
Material Specifications: Specifies the types of materials that can be used for the pipes, fittings, flanges, valves, and other components within the class, considering the chemical compatibility and mechanical properties needed for the service conditions.
Pressure-Temperature Ratings: Indicates the maximum pressure and temperature that the components in the class can withstand during operation. This is crucial for ensuring the safety and integrity of the piping system under different operating conditions.
Corrosion Allowance: Provides a specified amount of extra material thickness to account for expected corrosion over the service life of the piping system, ensuring that the components still meet the minimum requirements after some degree of corrosion.
Size Range: Details the range of sizes for the components within the class, including diameter and wall thickness, to accommodate different flow rates and pressures.
End Connections: Specifies the types of end connections (such as threaded, welded, or flanged) that are suitable for the components, ensuring proper connection and sealing between parts.
Component Types: Lists the types of components (e.g., pipes, elbows, tees, reducers, valves, gaskets) included in the class, ensuring that all necessary parts are standardized for compatibility and interchangeability.
Design Codes and Standards: References the applicable design codes and standards that the components must comply with, such as those from ASME (American Society of Mechanical Engineers), API (American Petroleum Institute), and ASTM (American Society for Testing and Materials).
Special Requirements: Any additional requirements specific to the application or service conditions, such as impact testing for low-temperature services, sour service specifications, or special coatings for corrosion protection.
WHO ISSUES PIPE CLASSES?
The responsibility for creating pipe classes typically falls to a multidisciplinary team within the organization that owns, operates, or designs the piping systems (an EPC, or an End-User). This team usually includes a mix of experienced professionals such as:
Piping Engineers: They play a central role in defining the pipe classes, utilizing their expertise in fluid mechanics, material science, and system design to specify the appropriate materials, pressure-temperature ratings, and other critical parameters for the piping components.
Process Engineers: These engineers contribute by providing information about the types of fluids (gas, liquid, corrosive nature, etc.), operating temperatures, and pressures that the piping system must handle, ensuring that the pipe class specifications meet the process requirements.
Materials Engineers: They advise on the selection of materials for the piping components based on their compatibility with the fluids being transported, their resistance to corrosion, and their suitability for the operating environment (temperature, pressure, external conditions).
Designers and Draftsmen: Once the specifications are determined, designers and draftsmen work on the detailed drawings and schematics, incorporating the pipe classes into the design of the piping systems.
Quality Assurance/Quality Control (QA/QC) Engineers: These professionals ensure that the pipe classes meet industry standards and regulatory requirements, conducting reviews and approvals of the specifications.
Project Managers: Oversee the integration of pipe classes into projects, ensuring that the specifications are adhered to during procurement, construction, and operation phases.
Additionally, organizations often adhere to industry standards and guidelines set by authoritative bodies like the American Society of Mechanical Engineers (ASME), American Petroleum Institute (API), and others. These standards help in forming a baseline for creating pipe classes, although specific requirements may be tailored to meet the unique needs of each project or facility.
In larger projects or operations, the creation and maintenance of pipe classes might also involve collaboration with external consultants or specialists who provide additional expertise or verification services to ensure that the pipe classes are appropriately designed and implemented.
DO PIPE CLASSES SPECIFY PIPES ONLY?
No, a pipe class encompasses not only pipes but also a wide range of other piping components such as fittings, valves, and flanges. The primary purpose of a pipe class is to ensure that all these components are compatible with each other and suitable for specific service conditions within a piping system. By defining a set of criteria that these components must meet, a pipe class facilitates the selection of materials and components that can safely and efficiently work together under the designated pressures, temperatures, and chemical conditions.

Here’s a closer look at how a pipe class typically includes specifications for various components:
Pipes: Specifies the material types, sizes (diameter and wall thickness), and the applicable standards for pipes used within the system.
Fittings: Includes elbows, tees, reducers, caps, and other fittings. The class specifies the materials, pressure ratings, dimensions, and standards that these fittings must meet to ensure they are compatible with the pipes and other components.
Valves: Details the types of valves (such as gate, globe, check, and ball valves), their material construction, pressure ratings, end connections, and dimensions. The inclusion of valves in the pipe class ensures that they can withstand the operational demands of the system.
Flanges: Specifies the type of flanges (weld neck, slip-on, blind, etc.), materials, pressure ratings, dimensions, and facing types (such as raised face or flat face). This ensures that the flanges can properly connect pipes and other components, providing a leak-proof system.
Gaskets: Though not always detailed as extensively as other components, gaskets are often included in pipe class specifications to ensure the selected materials are suitable for the intended fluid service and can withstand the system’s temperature and pressure conditions.
By including all these components, a pipe class acts as a comprehensive guide for designing and assembling piping systems, ensuring that all parts are appropriately matched and meet the necessary standards for safety, durability, and performance. This holistic approach is crucial in complex industrial applications such as in the oil & gas, power generation, and chemical manufacturing sectors, where the integrity of the piping system is paramount.
WHAT IS A PIPE SPECIFICATION?
A pipe specification, often abbreviated as “pipe spec,” is a document that provides detailed information about the technical requirements for the manufacture, fabrication, and testing of pipes used in a piping system. It outlines the dimensions, material grade, mechanical properties, and chemical compositions of the pipes, as well as any special requirements for specific applications.
Pipe specifications ensure that the pipes used in a project meet the necessary standards for safety, reliability, and performance. These specifications are often based on international standards (such as ASTM, ASME, and API) but can be tailored to meet the specific needs of a project or organization.
INFORMATION IN PIPE SPECIFICATIONS
Pipe specifications, often detailed documents, outline the technical requirements for pipes used in various applications, focusing primarily on their manufacture, design, and testing. These specifications are crucial for ensuring that pipes meet the necessary safety, performance, and regulatory standards. Typically, a pipe specification will cover the following information:
Material Grade: Specifies the type of material from which the pipe is made, such as carbon steel (e.g., ASTM A106), stainless steel (e.g., ASTM A312), or other specialized materials. The grade influences the pipe’s mechanical properties and chemical resistance.
Size and Dimensions: Details include the outer diameter (OD), inner diameter (ID), nominal size, and wall thickness (schedule). These dimensions are essential for ensuring the pipe can handle the required flow rates and pressures.
Manufacturing Process: Indicates whether the pipe is seamless or welded, affecting its strength and application. The specification might also include details on the fabrication process, such as electric resistance welding (ERW) or submerged arc welding (SAW).
Mechanical Properties: Covers the physical characteristics of the pipe material, including tensile strength, yield strength, elongation, and hardness. These properties ensure the pipe can withstand the operational stresses it will encounter.
Chemical Composition: Lists the permissible chemical makeup of the material, ensuring compatibility with the fluid being transported and corrosion resistance.
Pressure Rating: The maximum pressure the pipe can safely handle, often related to the material and wall thickness.
End Finishes: Describes the treatment of the pipe ends, such as plain, beveled for welding, or threaded, which affects how pipes are connected in a system.
Standards and Codes Compliance: References to applicable industry standards and codes (e.g., ASME, ASTM, API) that the pipe meets. Compliance ensures that the pipes are suitable for their intended application and meet global quality and safety benchmarks.
Testing and Certification Requirements: Specifies the types of tests the pipe must undergo before it is deemed fit for use, such as hydrostatic testing, ultrasonic testing, or X-ray inspection, along with any certification requirements.
Marking and Packaging: Instructions for how the pipe should be marked (e.g., manufacturer’s name, material grade, size) and any special packaging requirements for transport and storage.
This comprehensive information ensures that engineers and procurement specialists can select and use pipes that meet the precise requirements of their projects, ensuring safety, efficiency, and regulatory compliance.
WHO ISSUES PIPE SPECIFICATIONS?
Pipe specifications are issued by a variety of entities depending on the context in which they are used, including:
Standards Organizations: International and national standards bodies, such as the American Society for Testing and Materials (ASTM), American Petroleum Institute (API), and American Society of Mechanical Engineers (ASME), develop and issue widely recognized pipe specifications. These specifications are created through consensus processes involving experts in the field and are used globally across various industries to ensure the quality and safety of piping materials.
Industry Groups: Specific industry sectors may have groups or consortia that develop specialized pipe specifications tailored to their unique needs. These specifications address the particular challenges and requirements of industries like oil and gas, chemical manufacturing, or power generation.
Government and Regulatory Bodies: In some cases, government agencies or regulatory authorities issue pipe specifications to ensure compliance with safety, environmental, and health regulations. These specifications are legally binding within the jurisdiction they cover and must be adhered to by companies operating in those areas.
Individual Companies: Large engineering, procurement, and construction (EPC) firms, as well as companies in sectors like oil and gas, may develop their own internal pipe specifications for projects. These specifications are tailored to the company’s standards, project requirements, and past experiences, ensuring consistency and quality across their operations.
Engineering Firms: Engineering and design firms working on specific projects may issue pipe specifications as part of the project documentation. These specifications are developed based on the project’s technical requirements, client preferences, and applicable industry standards, ensuring that the piping system meets all necessary criteria for performance, safety, and reliability.
In summary, pipe specifications can come from a broad spectrum of sources, each bringing its expertise and perspective to ensure that piping materials meet the required standards for a given application. These specifications play a crucial role in the safe and efficient design, construction, and operation of piping systems across industries.
LEADING ISSUERS OF PIPE SPECIFICATIONS
In the United States
In the United States, several key organizations are instrumental in issuing specifications for pipes and related piping products. These specifications set the standards for dimensions, material properties, testing procedures, and applications to ensure safety, reliability, and compatibility across various industries. Here are some of the primary American organizations involved in this process:
American Society for Testing and Materials (ASTM International): ASTM is one of the leading standards organizations, developing and publishing voluntary consensus technical standards for a wide range of materials, products, systems, and services, including pipes and piping components.
American Petroleum Institute (API): API primarily serves the oil and natural gas industry. It issues standards for the design, manufacture, and testing of pipes and other equipment used in hydrocarbon production, refining, and distribution.
American Society of Mechanical Engineers (ASME): ASME is known for setting the codes and standards for the design, fabrication, and inspection of boilers and pressure vessels, which include extensive specifications for piping systems, through the ASME Boiler and Pressure Vessel Code (BPVC) and the B31 Piping Codes.
American Water Works Association (AWWA): AWWA focuses on water management and water treatment industries. It provides standards for water pipes, valves, and other components used in water and wastewater treatment systems.
National Association of Corrosion Engineers (NACE International): Though NACE’s focus is broader than just piping, it issues standards related to corrosion control, which includes specifications for materials and coatings used in piping systems exposed to corrosive environments.
Manufacturers Standardization Society (MSS): MSS specializes in the standardization of piping components such as valves, fittings, and flanges. It publishes standards that complement those of ASME and other organizations.
In Europe
In Europe, several key organizations issue specifications and standards for pipes and piping components, contributing to the harmonization of quality, safety, and efficiency across various industries. Some of these organizations include:
CEN (European Committee for Standardization): CEN is a major provider of European Standards (EN) and technical specifications in a wide range of fields, including piping systems. EN standards ensure compatibility and interoperability within the European Single Market.
EIGA (European Industrial Gases Association): While EIGA primarily focuses on the industrial and medical gases sector, it issues guidelines and standards that include specifications for piping systems used in gas applications.
DIN (Deutsches Institut für Normung): The German national organization for standardization, which has developed a vast array of standards, including those for piping systems. DIN standards are widely recognized and used not only in Germany but internationally.
BSI (British Standards Institution): The UK’s national standards body, which publishes British Standards. BSI provides specifications for a wide range of products and services, including piping systems.
AFNOR (Association Française de Normalisation): The French national organization for standardization, issuing NF standards covering various aspects of piping systems among other sectors.
UNI (Ente Nazionale Italiano di Unificazione): The Italian standards organization, which provides UNI standards applicable to piping systems among other fields.
CEN/CENELEC: While CEN focuses on standardization in non-electrical fields, CENELEC (European Committee for Electrotechnical Standardization) deals with electrical fields. Together, they work to harmonize standards across Europe, including those related to piping systems where applicable.
In Japan
In Japan, several organizations play pivotal roles in issuing specifications and standards for pipes and piping components, contributing to the country’s technological advancement and ensuring safety, efficiency, and quality in various industries. Some of these organizations include:
JIS (Japanese Industrial Standards) Committee: The JIS Committee, operating under the Japanese Industrial Standards Act, formulates standards for industrial methods, processes, and products in Japan, including pipes and piping systems. JIS standards are comprehensive and cover a wide range of materials, product specifications, and quality benchmarks.
JPI (Japan Petroleum Institute): Focused on the oil and gas industry, JPI issues standards and specifications that include those for pipes and piping components used in petroleum exploration, extraction, refining, and distribution.
JWWA (Japan Water Works Association): JWWA develops standards for water service, including pipes and fittings used in water supply systems. Their standards ensure the safety and reliability of drinking water infrastructure.
JSA (Japanese Standards Association), also known as JISC (Japanese Industrial Standards Committee), plays a central role in standardizing various industrial processes and products, including those related to piping systems.
These organizations ensure that piping and related components manufactured or used in Japan meet strict criteria for performance, reliability, and safety. By adhering to these standards, Japanese industries can maintain high levels of quality and innovation in their products and services.
In Korea
In South Korea, several authoritative bodies are responsible for developing and issuing specifications and standards for pipes and related piping components. These organizations play a crucial role in ensuring the quality, safety, and efficiency of piping systems across various industries. Some of the primary organizations include:
KATS (Korean Agency for Technology and Standards): KATS is a government agency under the Ministry of Trade, Industry and Energy (MOTIE) and is the national standards body of South Korea. It is responsible for establishing and maintaining standards, including those for pipes and piping systems, through the Korean Industrial Standards (KS).
KOSHA (Korea Occupational Safety and Health Agency): While primarily focused on occupational safety, KOSHA also contributes to setting safety standards related to industrial equipment and infrastructure, which includes piping systems, especially in terms of installation, inspection, and maintenance.
KGS (Korea Gas Safety Corporation): Specializing in the gas industry, KGS sets standards and conducts inspections for gas facilities, including piping systems used in gas distribution and utilization. They ensure that the infrastructure is safe and compliant with regulatory requirements.
KSSC (Korean Standards and Specifications Commission): This commission plays a pivotal role in the formulation and publication of national standards, including those related to piping and tubing, ensuring that these materials meet high-quality standards for various applications.
These organizations collectively contribute to the development, regulation, and enforcement of pipe specifications in South Korea, ensuring that materials and practices meet both national and international standards for quality and safety. Their standards cover a wide range of materials and applications, from industrial and construction to energy and utilities, reflecting the diverse needs of the South Korean economy.
In China
In China, several authoritative organizations are responsible for issuing specifications and standards for pipes and piping systems, overseeing the quality, safety, and efficiency of these components across various sectors. Key organizations include:
SAC (Standardization Administration of China): SAC is the national standards body of China, responsible for developing and issuing national standards (GB and GB/T standards) that include specifications for pipes and piping systems. These standards are critical for ensuring product quality and safety across a wide range of industries.
CNSA (China National Standards Association): While SAC is the primary body, CNSA plays a significant role in the coordination and promotion of the standardization strategy in China, including standards related to piping.
CST (China Iron and Steel Association): CST issues standards and provides guidance for the steel industry, including specifications for steel pipes used in construction, oil and gas, and other sectors.
CPCIA (China Petroleum and Chemical Industry Association): This association is involved in setting standards for the chemical and petroleum industries, including specifications for pipes and fittings used in the transport and processing of chemical and petroleum products.
CAQSIQ (General Administration of Quality Supervision, Inspection and Quarantine): Before its merger into the State Administration for Market Regulation (SAMR), CAQSIQ was responsible for quality control, including the certification and regulation of products like piping systems. SAMR now continues this role, ensuring that products meet China’s standards for quality, safety, and performance.
These organizations ensure that piping systems in China adhere to rigorous standards, promoting innovation, safety, and interoperability within domestic and international markets.
DOES THE CONCEPT OF SPECIFICATION APPLY TO OTHER PIPING PRODUCTS?
Sure! Specifications for other piping products, aside from pipes themselves, are typically referred to based on the specific product they describe, often following a structured naming convention that identifies the type of component and its standardization criteria.
Here’s how these specifications are generally categorized and named:
Fittings Specifications: These detail the requirements for piping fittings such as elbows, tees, reducers, and caps, covering aspects like material grades, dimensions, pressure ratings, and end connections. They ensure fittings are compatible with pipes and can withstand the system’s operational conditions (for example ASME B16.19).
Valve Specifications: Outline the types, materials, sizes, pressure ratings, and operational functionalities of valves used in piping systems. Valves control the flow and pressure within the system, so their specifications are crucial for ensuring reliable and safe operation (for example, API 6D).
Flange Specifications: Provide details on the types of flanges (weld neck, slip-on, threaded, etc.), material grades, dimensions, pressure classes, and face types. Flange specifications ensure a proper seal and fit between pipe sections and other components (for example, ASME/ANSI B16.5).
Gasket Specifications: Define the types (spiral wound, ring joint, etc.), materials, dimensions, and application conditions for gaskets, which are critical for achieving leak-proof seals at flanged connections (like ASME B16.21).
Bolt and Nut Specifications: These specify the materials, dimensions, strength grades, and coatings for bolts and nuts used to secure flanged connections, ensuring structural integrity and leak prevention (like ASTM A193).
Each of these product specifications plays a crucial role in the design, selection, and installation of piping systems, ensuring that all components work together effectively to transport fluids safely and efficiently. Like pipe specifications, these product-specific specifications often adhere to international, national, or industry standards and may be developed by standards organizations (such as ASTM, ASME, API), regulatory bodies, or individual companies to meet specific project or operational needs.
DIFFERENCES BETWEEN PIPE CLASS VS. PIPE SPECIFICATION
Understanding the distinctions between pipe class and pipe specification is fundamental in the fields of piping design, engineering, and construction.
Though both terms are closely related to the selection and use of pipes and their components in various industries, they serve different purposes and encompass different scopes of information. Here’s a detailed comparison to clarify the differences:
PURPOSE
Pipe Class
- A pipe class is a categorized grouping of piping materials that share common design and construction standards. It is essentially a classification system that defines a set of components (pipes, fittings, valves, and other piping materials) based on similar operating conditions, material types, and pressure-temperature ratings.
- The primary purpose of a pipe class is to ensure compatibility and standardization among the components used in piping systems. It simplifies the selection process for engineers and designers by providing a predefined set of criteria that align with specific operational requirements.
Pipe Specification (Pipe Spec)
- A pipe specification provides detailed technical requirements for the manufacture, fabrication, and testing of pipes. It focuses on the physical and chemical properties of the pipe materials, including dimensions, material grades, mechanical properties, and manufacturing processes.
- The main goal of a pipe specification is to ensure that pipes meet the necessary quality, performance, and compliance standards for their intended application. It acts as a guideline for manufacturers and suppliers to produce pipes that are suitable for specific operational conditions.
SCOPE
Pipe Class
- Specifies a broad range of piping components, not limited to pipes alone. It includes fittings, flanges, valves, and other accessories.
- Outlines material specifications, pressure-temperature ratings, corrosion allowances, and end connections suitable for the components within the class.
- May reference applicable design codes and standards that the components must comply with.
Pipe Specification
- Specifically targets pipes, providing detailed technical and mechanical properties required for their manufacture.
- Includes precise dimensions (e.g., outer diameter, wall thickness), material grades, chemical compositions, and mechanical properties (e.g., tensile strength, yield strength).
- Details the manufacturing process (e.g., seamless, welded), testing requirements (e.g., hydrostatic test, ultrasonic test), and standards compliance (e.g., ASTM, ASME).
APPLICATIONS & USES
Pipe Class
- Used by engineers and designers in the initial stages of a project to select and specify piping components that are compatible and suitable for the overall piping system design.
- Facilitates the standardization of piping materials across projects, ensuring that all selected components work together efficiently and safely.
Pipe Specification
- Utilized by manufacturers, fabricators, and quality control teams to ensure that pipes are produced according to specific technical requirements.
- Provides a basis for testing and certifying pipes, ensuring they are fit for purpose before being incorporated into a piping system.
In essence, a pipe class serves as a comprehensive guideline for the selection of compatible piping components within a system, ensuring they meet the required service conditions. In contrast, a pipe specification provides detailed manufacturing and quality criteria for pipes, focusing on their physical and chemical properties to ensure compliance with industry standards and project requirements. Both are integral to the design, construction, and maintenance of safe and efficient piping systems.