What are OCTG pipes? Oil country tubular goods are pipes used for onshore and offshore oil & gas upstream operations (extract oil and gas from the wellbore). OCTG pipes may be classified into three main families: drill pipes (to perforate the soil and reach the reserve), casing pipes (to consolidate the well and prepare it for the actual extraction), and tubing pipes (to extract the product from the ground to the surface). API 5CT is the reference specification for OCTG pipes.
TYPES OF OCTG PIPE
First, OCTG is the acronym for “Oil Country Tubular Goods” – i.e. pipes for oil (and gas) extraction from the soil. The three main OCTG pipe types are:
- Casing pipes are used to stabilize the wellbore. A casing pipe is subject to axial tensions and to internal pressures generated by the pumped oil or gas, by their heavyweight and the external pressures coming from the surrounding rocks
- Tubing pipes are tubular goods through which the oil or gas is transported from the wellbore to the surface. Tubing segments are generally around 30′ long with a threaded connection on each end (standard or premium connections are available)
- Drill pipes are heavyweight seamless tubular that rotate the drill bit and circulate the drilling fluid. Pipe segments of 30′ are coupled with tool joints. Drill pipe is subject to high torque by drilling, axial tension by weight, and internal pressure due to the purging of the drilling fluid. Additionally, alternating bending loads due to non-vertical or deflected drilling may be superimposed on these basic loading patterns
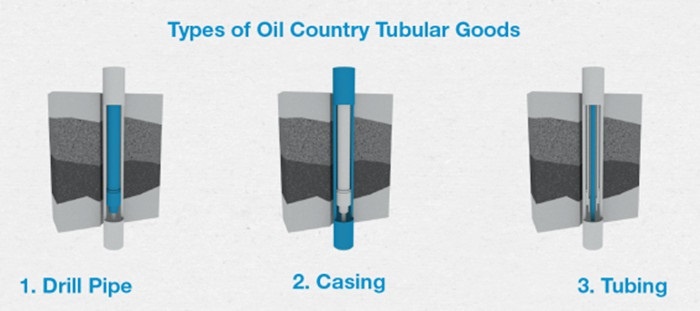
The API 5CT specification covers seamless and welded casing and tubing pipes for upstream operations (pipes that belong to the OCTG family, as illustrated above).
Let’s review each type of OCTG pipe more in detail.
OCTG “CASING” PIPES
OCTG casing pipes, short for Oil Country Tubular Goods casing pipes, are specialized steel pipes used primarily in the oil and gas industry for the exploration, drilling, and production of hydrocarbons. These pipes serve as structural components in oil and gas wells, providing support to the wellbore and facilitating the extraction of oil and natural gas from underground reservoirs. Here’s a comprehensive overview of OCTG casing pipes:
1. Function and Importance
- OCTG casing pipes are an integral part of oil and gas well construction, serving multiple functions:
- Providing structural support to the wellbore and preventing it from collapsing under the pressure of surrounding formations.
- Sealing off the wellbore from surrounding formations to prevent the migration of fluids and gases.
- Facilitating the installation of downhole equipment such as production tubing, packers, and pumps.
- Casing pipes play a crucial role in ensuring the integrity and efficiency of oil and gas wells, allowing for safe and efficient production operations.
OCTG casing pipes are a key structural component for an oil & gas well and have the following scope:
- Keep the borehole stability in the well
- Prevent the bore contamination from water sands
- Prevent water from producing formations
- Exercise tight control of the wellbore pressures during the drilling, production, and repair operations
Casing pipes are used to install:
- Blowout Preventers (BOP)
- Other wellhead equipment necessary to extract hydrocarbons
- Production tubing and packers
2. Construction and Materials
- OCTG casing pipes are typically made of high-strength, corrosion-resistant steel alloys such as carbon steel, alloy steel, or stainless steel.
- These pipes are manufactured using specialized processes such as seamless extrusion or electric resistance welding (ERW) to ensure uniformity, strength, and dimensional accuracy.
- Casing pipes are available in various sizes, grades, and specifications to suit different well conditions, depths, and environments.
3. Types of OCTG Casing Pipes
- Conventional Casing: Standard casing pipes used in conventional oil and gas wells, typically ranging from 4.5 inches to 20 inches in diameter.
- Premium Casing: High-performance casing pipes with enhanced properties such as corrosion resistance, high collapse resistance, and improved connection designs. Premium casing is often used in challenging well environments such as deepwater, high-pressure, and high-temperature wells.
- Threaded and Coupled Casing: Casing pipes equipped with threaded connections for easy installation and removal during well construction. These connections ensure a secure seal and allow for efficient makeup and breakout operations.
4. Grades and Specifications
- OCTG casing pipes are classified into different grades based on their mechanical properties, chemical composition, and performance characteristics.
- Common casing grades include API 5CT grades such as H40, J55, K55, N80, L80, C90, T95, P110, and Q125, each designed for specific well conditions and operating requirements.
- Specifications for OCTG casing pipes are established by organizations such as the American Petroleum Institute (API) and international standards organizations to ensure quality, consistency, and compatibility with well equipment and procedures.
5. Installation and Use
- Casing pipes are installed sequentially during the drilling process, with each section of pipe being lowered into the wellbore and connected to the previous section using threaded connections.
- Once installed, casing pipes are cemented in place to provide additional support and seal off the annular space between the casing and the surrounding formations.
- Casing pipes remain in place throughout the life of the well, serving as a permanent conduit for the extraction of oil and gas and providing structural integrity to the wellbore.
6. Challenges and Considerations
- Designing and selecting the appropriate casing string for a well requires careful consideration of factors such as well depth, formation characteristics, reservoir pressure, temperature, and fluid properties.
- Operators must also adhere to regulatory requirements and industry best practices to ensure the safe and environmentally responsible construction and operation of oil and gas wells.
7. Sizes and End-Connections
Casing pipes are available in a diameter range 4 1/2 to 20 inches, and in the following materials: H-40, J-55, K-55, N-80, L-80/C, 90/T, 95, P110, Q-125 – as discussed in more detail below.
The main types of connections for casing pipes are STC (short threads), LTC (long threads), BTC (buttress threads), and premium gas-tight connections.
In summary, OCTG casing pipes are essential components in the oil and gas industry, providing structural support, fluid containment, and well integrity in the exploration, drilling, and production of hydrocarbons. With their robust construction, diverse specifications, and critical role in well construction and operation, casing pipes play a vital role in the global energy sector, supporting the extraction of oil and gas resources from the earth’s subsurface.
Casing pipes are also one major individual component of the overall cost of the well, therefore the correct selection of the casing size, materials, connectors, and depth shall be at the top of design engineers (for cost and efficiency reasons).
The six basic types of casing strings are:
- Conductor Casing
- Surface Casing
- Intermediate Casing
- Production Casing
- Liner
- Liner tieback casing
Oilfield casing pipes are positioned into the wellbore and cemented in place to secure both subsurface formations and the wellbore from collapsing, and also to enable drilling mud to circulate and extraction to take place.
The strict quality requirement for steel is due to the harsh working conditions of the casing.
The steel product should be produced and checked following special standards or specifications. ISO 11960 and API Spec 5CT have specified the steel product standards of the casing.
OCTG “TUBING” PIPES
OCTG tubing pipes, also known as Oil Country Tubular Goods tubing pipes, are specialized steel pipes used in the oil and gas industry for the production and transportation of oil, natural gas, and other fluids from underground reservoirs to the surface. These pipes are an essential component of oil and gas well completion and production systems, providing a conduit for the extraction of hydrocarbons from the reservoir to the surface facilities. Here’s a comprehensive overview of OCTG tubing pipes:
1. Function and Importance
• OCTG tubing pipes are designed to convey oil, natural gas, and production fluids from the reservoir to the surface during well production operations.
• They serve as a conduit for the passage of fluids, providing a pathway for the flow of hydrocarbons from the downhole reservoir to the surface processing facilities.
• Tubing pipes also play a crucial role in supporting and protecting the production tubing and downhole equipment such as pumps, packers, and sensors.
Tubing pipes are used to bring oil and gas from the underground reserves up to the field for further processing. Tubing pipes need resistance to mechanical stress as they are subject to very high loads and deformations during production operations. In addition, tubing pipe sizes should be properly calculated to support the expected oil and gas flow from the ground to the surface (a too-small diameter would decrease the production rate and the return on investment on the wellbore licenses, whereas too-large tubing would generate non-recoverable costs due to the greater amount of steel used for the bore construction vs. the actual requirement (steel for the casing and tubing pipes).
2. Construction and Materials
• OCTG tubing pipes are typically made of high-strength, corrosion-resistant steel alloys such as carbon steel, alloy steel, or stainless steel.
• These pipes are manufactured using specialized processes such as seamless extrusion or electric resistance welding (ERW) to ensure uniformity, strength, and dimensional accuracy.
• Tubing pipes are available in various sizes, grades, and specifications to suit different well conditions, depths, and environments.
3. Types of OCTG Tubing Pipes
• Conventional Tubing: Standard tubing pipes used in conventional oil and gas wells, typically ranging from 2.375 inches to 4.5 inches in diameter.
• Premium Tubing: High-performance tubing pipes with enhanced properties such as corrosion resistance, high collapse resistance, and improved connection designs. Premium tubing is often used in challenging well environments such as deepwater, high-pressure, and high-temperature wells.
• Coiled Tubing: Continuous lengths of small-diameter tubing wound onto a spool for use in well intervention and workover operations. Coiled tubing offers advantages such as faster installation, reduced rig time, and improved access to deviated and horizontal wellbores.
4. Grades and Specifications
• OCTG tubing pipes are classified into different grades based on their mechanical properties, chemical composition, and performance characteristics.
• Common tubing grades include API 5CT grades such as J55, K55, N80, L80, C90, T95, P110, and Q125, each designed for specific well conditions and operating requirements.
• Specifications for OCTG tubing pipes are established by organizations such as the American Petroleum Institute (API) and international standards organizations to ensure quality, consistency, and compatibility with well equipment and procedures.
5. Installation and Use
• Tubing pipes are installed inside the casing strings during the completion of an oil or gas well, forming a continuous conduit for the flow of production fluids from the reservoir to the surface.
• Once installed, tubing pipes are connected to downhole equipment such as pumps, packers, and safety valves to facilitate the production and monitoring of the well.
• Tubing pipes remain in place throughout the life of the well, allowing for the continuous production of oil and gas and providing access for well intervention and maintenance activities.
6. Challenges and Considerations
• Designing and selecting the appropriate tubing string for a well requires consideration of factors such as reservoir characteristics, production rates, fluid properties, and wellbore conditions.
• Operators must also adhere to regulatory requirements and industry best practices to ensure the safe and efficient production and operation of oil and gas wells.
7. Sizes, Materials, End-Connections
Tubing pipes are manufactured in seamless and welded execution, in the size range of 1.050 to 5 1/2 inches (consult this article to see the AP5CT tubing pipes sizes) and in the following material grades: H-40, J-55, K-55, N-80, L-80, C-90, T-95, P-110, Q-125 (more details about API 5CT tubing materials are in this article).
The main types of connections for tubing pipes are NUE (non-upset), EUE (external upset), and premium. Corrosion resistance under sour service conditions is a very important OCTG characteristic, especially for casing and tubing.
In summary, OCTG tubing pipes are essential components in the oil and gas industry, providing a conduit for the production and transportation of hydrocarbons from underground reservoirs to the surface. With their robust construction, diverse specifications, and critical role in well production operations, tubing pipes play a vital role in the global energy sector, supporting the extraction and production of oil and gas resources worldwide.
OCTG “DRILL” PIPES
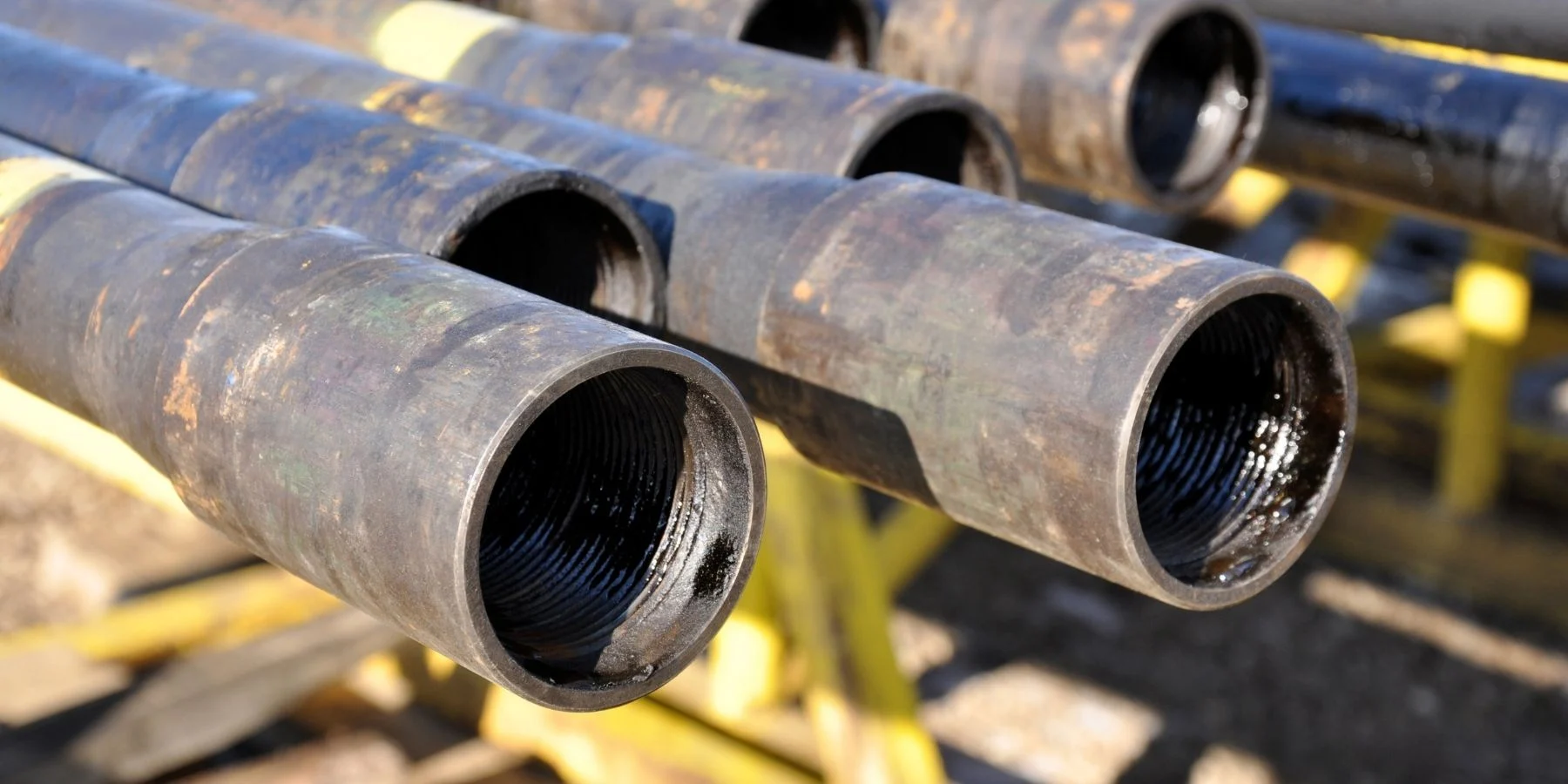
OCTG drill pipes, also known as Oil Country Tubular Goods drill pipes, are specialized tubular components used in the drilling of oil and gas wells. These pipes are an integral part of the drilling string, serving as a conduit for the transmission of drilling fluid, as well as providing structural support and torque transmission to the drilling assembly. Here’s a detailed overview of OCTG drill pipes:
1. Function and Importance
– OCTG drill pipes are designed to transmit drilling fluid from the surface to the drill bit at the bottom of the wellbore during the drilling process.
– They provide structural support to the drilling assembly and facilitate the rotation and movement of the drill bit, allowing for the penetration of the earth’s subsurface layers.
– Drill pipes also serve as a conduit for the extraction of rock cuttings and debris from the wellbore to the surface, helping to maintain the integrity of the drilling operation.
2. Construction and Materials
– OCTG drill pipes are typically made of high-strength, alloyed steel to withstand the rigors of drilling operations and the harsh downhole conditions encountered in oil and gas wells.
– These pipes are manufactured using specialized processes such as seamless extrusion or electric resistance welding (ERW) to ensure uniformity, strength, and dimensional accuracy.
– Drill pipes are available in various sizes, lengths, and specifications to suit different drilling environments, depths, and applications.
3. Design and Components
– Drill pipes consist of several components, including the pipe body, tool joints, and threads.
– The pipe body is the main cylindrical section of the drill pipe, while the tool joints are the thicker, threaded ends that connect adjacent sections of pipe.
– Tool joints are designed to withstand high loads, torque, and bending stresses encountered during drilling operations and are typically made of hardened steel for increased durability.
– Threads are machined onto the tool joints to allow for the connection and disconnection of drill pipe sections, as well as the attachment of other drilling tools and equipment.
4. Specifications and Grades
– OCTG drill pipes are classified into different grades based on their mechanical properties, chemical composition, and performance characteristics.
– Common drill pipe grades include API 5DP grades such as E75, X95, G105, and S135, each designed for specific drilling conditions, formations, and operating requirements.
– Specifications for OCTG drill pipes are established by organizations such as the American Petroleum Institute (API) and international standards organizations to ensure quality, consistency, and compatibility with drilling equipment and procedures.
5. Installation and Use
– Drill pipes are assembled into a drilling string and lowered into the wellbore using a drilling rig.
– The drill pipes are connected end-to-end using threaded connections and are rotated and pushed downward to advance the drill bit into the earth’s subsurface layers.
– Drilling fluid, also known as mud, is pumped through the drill pipes to cool the drill bit, carry rock cuttings to the surface, and provide hydraulic pressure to stabilize the wellbore.
6. Maintenance and Inspection
– Drill pipes undergo regular inspection and maintenance to ensure their integrity and performance during drilling operations.
– Inspection methods may include visual examination, dimensional checks, ultrasonic testing (UT), magnetic particle testing (MT), and other non-destructive testing (NDT) techniques to detect defects, cracks, and wear.
In summary, OCTG drill pipes play a critical role in the drilling of oil and gas wells, serving as conduits for drilling fluid, structural support for the drilling assembly, and transmission of torque to the drill bit. With their robust construction, diverse specifications, and vital function in the drilling process, drill pipes are essential components in the exploration and production of oil and gas resources worldwide.
OCTG PIPE MANUFACTURING PROCESS
The manufacturing process of OCTG (Oil Country Tubular Goods) pipes involves several steps to produce high-quality steel pipes suitable for use in the oil and gas industry. This process typically includes the following stages:
1. Steel Making
• The manufacturing process begins with the production of steel from raw materials such as iron ore, coal, and other alloying elements.
• Steel making may involve processes such as a basic oxygen furnace (BOF), electric arc furnace (EAF), or continuous casting, depending on the desired properties of the final product.
2. Billet Production
• Once the steel is produced, it is cast into solid cylindrical shapes called billets through continuous casting or casting molds.
• Billets serve as the starting material for the subsequent manufacturing steps in the production of OCTG pipes.
3. Pipe Manufacturing
• The billets are heated to high temperatures in a furnace to make them more malleable and easier to deform.
• The heated billets are then subjected to forging or extrusion processes to form seamless pipes. For welded pipes, the billets may be hot rolled into strip coils, which are subsequently formed into welded pipes through processes such as ERW (Electric Resistance Welding) or SAW (Submerged Arc Welding).
• For seamless pipes, the forged or extruded hollow blanks are further elongated and reduced in diameter through multiple rolling passes to achieve the desired dimensions and wall thickness.
4. Heat Treatment
• After the pipes are formed, they undergo heat treatment processes such as annealing, normalizing, or quenching and tempering to improve their mechanical properties and microstructure.
• Heat treatment helps to relieve internal stresses, refine the grain structure, and enhance the strength, toughness, and ductility of the pipes.
5. Surface Finishing
The pipes may undergo surface finishing processes such as shot blasting, pickling, or coating application to remove surface defects, improve corrosion resistance, and enhance appearance.
6. Testing and Inspection
• Throughout the manufacturing process, OCTG pipes undergo rigorous testing and inspection to ensure quality and conformance to specifications.
• Testing methods may include non-destructive testing (NDT) techniques such as ultrasonic testing (UT), magnetic particle testing (MT), radiographic testing (RT), and hydrostatic testing (HYT), as well as dimensional inspection and visual examination.
7. Marking and Identification
Once the pipes pass all quality checks and inspections, they are marked with relevant information such as size, grade, heat number, and manufacturer’s identification for traceability and identification purposes.
8. Packaging and Shipping
Finally, the finished OCTG pipes are carefully packaged for transportation and storage, typically in bundles or wooden crates, to protect them from damage during transit and handling.
In summary, the manufacturing process of OCTG pipes involves steel making, billet production, pipe manufacturing, heat treatment, surface finishing, testing and inspection, marking and identification, and packaging and shipping. By following stringent quality control measures and adhering to industry standards and specifications, manufacturers can produce high-quality OCTG pipes suitable for use in the demanding environments of the oil and gas industry.
To further understand the manufacturing processes of OCTG casing and tubing pipes the following should be taken into consideration:
- The continuous mandrel-rolling process and the push bench process are used for sizes between 21 and 178 mm OD.
- Plug mill rolling is used for sizes between 140 and 406 mm OD.
- Cross-roll piercing and Pilger rolling are used for sizes between 250 and 660 mm OD.
These processes typically do not allow the thermo-mechanical processing customary for the strip and plate products used for welded pipes.
Therefore, the high-strength seamless pipe must be produced by increasing the alloying content in combination with a suitable heat treatment such as quench & tempering.
Meeting the fundamental requirement of a fully martensitic microstructure even at large pipe wall thickness requires good hardenability. Chrome (Cr) and Manganese (Mn) are the main alloying elements used to produce good hardenability in conventional heat-treatable steel.
However, the requirement for good sulfide stress cracking (SSC) resistance limits their use. Mn tends to segregate during continuous casting and can form large MnS inclusions that reduce hydrogen-induced cracking (HIC) resistance. Higher levels of Cr can lead to the formation of Cr7C3 precipitates with coarse plate-shaped morphology, which acts as hydrogen collectors and crack initiators.
Alloying with Molybdenum can overcome the limitations of Mn and Cr alloying. Mo is a much stronger hardener than Mn and Cr, so it can easily recover the effect of a reduced amount of these elements.
Traditionally, OCTG grades were carbon-manganese steels (up to the 55-KSI strength level) or Mo-containing grades up to 0.4% Mo. In recent years, deep well drilling and reservoirs containing contaminants that cause corrosive attacks have created a strong demand for higher-strength materials resistant to hydrogen embrittlement and SCC.
Highly tempered martensite is the structure most resistant to SSC at higher strength levels, and 0.75% is the Mo concentration that produces the optimum combination of yield strength and to SSC resistance.
OCTG PIPE SELECTION CRITERIA
Selecting the appropriate OCTG (Oil Country Tubular Goods) pipes for oil and gas wells is crucial to ensure the integrity, efficiency, and safety of drilling and production operations. Several factors should be considered when choosing OCTG pipes, including:
1. Well Conditions and Environment
– Evaluate the geological and reservoir conditions of the well, including formation type, depth, pressure, temperature, and fluid properties.
– Consider the anticipated downhole environment, such as corrosive fluids, high-pressure zones, sour gas (H2S), and high-temperature conditions, which may influence the selection of pipe materials and coatings.
2. Operating Requirements and Specifications:
– Determine the specific requirements and specifications for the well, including casing size, wall thickness, grade, length, and connection type (e.g., API or premium connections).
– Select OCTG pipes that meet industry standards and regulatory requirements, such as those set by the American Petroleum Institute (API) and international standards organizations.
3. Pipe Grade and Material:
– Choose the appropriate OCTG pipe grade based on the well conditions, operating parameters, and performance requirements.
– Consider factors such as mechanical properties (e.g., yield strength, tensile strength, hardness), corrosion resistance, collapse resistance, and fatigue resistance when selecting pipe grades.
– Evaluate the suitability of different pipe materials, such as carbon steel, alloy steel, and stainless steel, for the specific downhole environment and service conditions.
4. Connection Type and Performance:
– Select suitable pipe connections (e.g., threaded and coupled, integral premium connections) based on the oil & gas well design, completion method, and operational preferences.
– Consider the performance characteristics of pipe connections, including sealing integrity, tensile strength, torque capacity, and resistance to pressure and bending loads.
5. Premium vs. Conventional Pipes:
– Evaluate the benefits and trade-offs of premium OCTG pipes compared to conventional pipes, considering factors such as enhanced performance, reliability, and cost-effectiveness.
– Premium pipes may offer advantages such as improved corrosion resistance, high collapse resistance, enhanced connection designs, and extended service life, but they may come at a higher cost.
6. Cost and Budget Considerations:
– Assess the overall cost-effectiveness of OCTG pipe options, taking into account factors such as upfront procurement costs, lifecycle costs, and potential savings from improved performance and reliability.
– Balance the need for high-quality pipes with budget constraints and project economics to optimize value and minimize risks.
7. Supplier Reputation and Support:
– Choose reputable OCTG pipe manufacturers and suppliers with a track record of delivering high-quality products, reliable service, and technical support.
– Consider factors such as manufacturing capabilities, quality assurance processes, supply chain reliability, and customer service responsiveness when selecting suppliers.
8. Regulatory Compliance and Certification:
– Ensure that OCTG pipes comply with applicable industry standards, specifications, and regulations, such as API 5CT for casing and tubing products.
– Verify the authenticity of product certifications, test reports, and compliance documentation provided by suppliers to confirm product quality and traceability.
In summary, OCTG pipe selection involves careful consideration of oil well conditions, operating requirements, pipe properties, connection types, cost considerations, supplier reliability, and regulatory compliance. By taking a systematic approach to pipe selection and leveraging industry expertise and best practices, operators can choose the most suitable OCTG pipes to meet their specific needs and ensure the success of oil and gas drilling and production projects.
OCTG PIPE MANUFACTURERS
The main manufacturers of OCTG pipes are listed below:
TUBOS REUNIDOS (Spain)
Tubos Reunidos is a Spanish manufacturer specializing in seamless steel pipes, including OCTG products. They offer a wide range of casing and tubing solutions for the oil and gas sector.
Vallourec (France)
Despite its troubled situation in the last few years, Vallourec is a major player in the OCTG industry. The company manufactures and distributes drill, casing, and tubing pipes with premium connections.
Tenaris (Italy & Argentina)
Tenaris is based in Argentina and manufactures a wide range of mechanical, structural, process, and OCTG pipes. In the OCTG area, Tenaris supplies drilling, casing, and tubing pipes with standard and premium connections, and other tubular equipment for upstream operations (such as sucker rods and coil tubes). Tenaris produces OCTG pipes in most major API grades, including carbon, alloy, and higher grades. Besides being a mill, Tenaris is also involved in contracting and consulting in upstream, midstream, and downstream oil & gas.
US Steel Tubular Products (USA)
US Steel is a multinational steel company covering a wide range of industries, from food to oil and gas. The company has a key role in the OCTG industry, as it produces drill, casing, and tubing pipes API 5CT in most sizes and API material grades with different types of commercial and proprietary connections.
Evraz North America (USA)
Evraz North America is a leading producer of OCTG pipes in North America, offering a variety of casing and tubing solutions for oil and gas applications.
Nippon Steel CORP. and Sumitomo (Japan)
Nippon Steel is an accredited supplier of OCTG pipes, used throughout the world and recognized for their exceptional quality. The company has been very active in developing stronger materials and innovative connections. Further, the company has a well-established distribution business, able to support exploration and upstream activities in real time.
JFE Steel Corporation (Japan)
JFE Steel Corporation is a Japanese steelmaker known for its high-performance steel products, including OCTG pipes. They offer a variety of casing and tubing solutions for the oil and gas industry.
TMK GROUP (Russia)
TMK is one of the top five pipe manufacturers in the world. Besides process pipes, TMK manufactures and distributes seamless and welded OCTG pipes in various material grades through a consolidated network of regional offices.
SeAH Steel Corporation (South Korea)
SeAH Steel Corporation is a South Korean manufacturer of steel pipes, including OCTG products. They supply casing, tubing, and line pipes to customers worldwide.
Arcelor Mittal (India)
Arcelor Mittal, a giant Indian/French steel conglomerate, is involved in the production and distribution of OCTG pipes for exploration and extraction operations. The Arcelor Mittal pipe and tubes division represents a small fraction of the whole company turnover (definitely less than 5%) but can still be considered one of the major players in the oil exploration and upstream industries.
Jindal Steel & Power Ltd. (India)
Jindal Steel & Power Ltd. is an Indian steel manufacturer producing OCTG pipes for the oil and gas sector. They offer a comprehensive range of casing and tubing products.
BORUSAN MANNESMANN (Turkey)
Borusan Mannesmann is a Turkish manufacturer of welded steel pipes, including OCTG products. They provide casing, tubing, and line pipes for oil and gas exploration and production.
Chinese Manufacturers of OCTG Pipes
Several Chinese manufacturers specialize in the production of OCTG (Oil Country Tubular Goods) pipes, catering to both domestic and international markets. Here are some notable Chinese manufacturers of OCTG pipes:
1. Baosteel Group Corporation: Baosteel Group Corporation, also known as Baowu Steel, is one of the largest steel producers in China. They manufacture a wide range of OCTG products, including casing, tubing, and drill pipes, for the oil and gas industry.
2. TPCO (Tianjin Pipe Corporation): TPCO is a leading manufacturer of seamless steel pipes, including OCTG products, based in Tianjin, China. They produce casing, tubing, and line pipes for various applications, serving customers worldwide.
3. Hengyang Valin Steel Tube Co., Ltd.: Hengyang Valin Steel Tube Co., Ltd. is a subsidiary of Valin Group, specializing in the production of seamless steel tubes, including OCTG pipes. They offer a comprehensive range of casing, tubing, and drill pipes for the oil and gas sector.
4. Panyu Chu Kong Steel Pipe Co., Ltd.: PCK is a leading manufacturer of longitudinally welded steel pipes, including OCTG products, based in Guangzhou, China. They supply casing, tubing, and line pipes to customers in the oil and gas industry.
5. Jiangsu Changbao Steel Tube Co., Ltd.: Changbao Steel Tube is a major manufacturer of seamless steel pipes, including OCTG products, located in Jiangsu Province, China. They produce casing, tubing, and drill pipes for oil and gas exploration and production.
6. Jiangsu Yulong Steel Pipe Co., Ltd.: Yulong Steel Pipe is a subsidiary of Yulong Group, specializing in the production of seamless steel pipes, including OCTG products. They supply casing, tubing, and line pipes for various applications in the oil and gas industry.
7. Jiangsu Tiancheng Group Limited: Tiancheng Group is a prominent manufacturer of seamless steel pipes, including OCTG products, based in Jiangsu Province, China. They offer a wide range of casing, tubing, and line pipes for oil and gas applications.
8. Zhejiang Zhongkuang Steel Pipe Co., Ltd.: Zhongkuang Steel Pipe is a leading manufacturer of seamless steel pipes, including OCTG products, located in Zhejiang Province, China. They provide casing, tubing, and drill pipes for the oil and gas sector.
9. Tianjin Dalipu Oil Country Tubular Goods Co., Ltd.: Dalipu Oil Country Tubular Goods is a specialized manufacturer of OCTG products, including casing, tubing, and drill pipes, based in Tianjin, China. They serve customers in the oil and gas industry both domestically and internationally.
10. Shengli Oil & Gas Pipe Holdings Limited: Shengli Oil & Gas Pipe Holdings is a major manufacturer of OCTG products in China, producing casing, tubing, and line pipes for oil and gas exploration and production. They are headquartered in Shandong Province, China.
These Chinese manufacturers are known for producing high-quality OCTG pipes that meet international standards and specifications, and they play a significant role in supplying tubular products to the global oil and gas industry.
OCTG PIPE DIMENSIONS
OCTG CASING PIPE SIZES
Note: P = plain end, S = short round thread, L = long round thread, B = buttress thread. Sizes per API 5CT specification
Source: API – American Petroleum Institute
OCTG Pipe Sizes (Casing) API5CT | Weight Lbs/ft | Outside Diameter | Wall Thickness | Type End Finish | |||||||||
Grade | |||||||||||||
ln. | mm | ln. | mm | H-40 | J-55 K-55 | M-65 | L-80C-95 | N-80 | C-90T-95 | P-110 | Q-125 | ||
7 5/8” | 24.00 | 7.625 | 193.68 | 0.300 | 7.62 | PS | — | — | — | — | — | — | — |
26.40 | 7.625 | 193.68 | 0.328 | 8.33 | — | PSLB | PSLB | PLB | PLB | PLB | PLB | — | |
29.70 | 7.625 | 193.68 | 0.375 | 9.53 | — | — | PLB | PLB | PLB | PLB | PLB | — | |
33.70 | 7.625 | 193.68 | 0.430 | 10.92 | — | — | PLB | PLB | PLB | PLB | PLB | — | |
39.00 | 7.625 | 193.68 | 0.500 | 12.70 | — | — | — | PLB | PLB | PLB | PLB | PLB | |
42.80 | 7.625 | 193.68 | 0.562 | 14.27 | — | — | — | PLB | PLB | PLB | PLB | PLB | |
45.30 | 7.625 | 193.68 | 0.595 | 15.11 | — | — | — | PLB | PLB | PLB | PLB | PLB | |
47.10 | 7.625 | 193.68 | 0.625 | 15.88 | — | — | — | PLB | PLB | PLB | PLB | PLB | |
51.20 | 7.625 | 193.68 | 0.687 | 17.45 | — | — | — | — | — | P | — | — | |
55.30 | 7.75 | 193.68 | 196.85 | 19.05 | — | — | — | — | — | P | — | — | |
7 3/4” | 46.10 | 8.625 | 219.08 | 0.595 | 15.11 | — | — | — | P | P | P | P | P |
8 5/8” | 24.00 | 8.625 | 219.08 | 0.264 | 6.71 | — | PS | PS | — | — | — | — | — |
28.00 | 8.625 | 219.08 | 0.304 | 7.72 | PS | — | PS | — | — | — | — | — | |
32.00 | 8.625 | 219.08 | 0.352 | 8.94 | PS | PSLB | PSLB | — | — | — | — | — | |
36.00 | 8.625 | 219.08 | 0.400 | 10.16 | — | PSLB | PSLB | PLB | PLB | PLB | PSLB | — | |
40.00 | 8.625 | 219.08 | 0.450 | 11.43 | — | — | PLB | PLB | PLB | PLB | PLB | — | |
44.00 | 8.625 | 219.08 | 0.500 | 12.70 | — | — | PLB | PLB | PLB | PLB | PLB | — | |
49.00 | 9.625 | 244.48 | 0.557 | 14.15 | — | — | — | PLB | PLB | PLB | PLB | PLB | |
9 5/8” | 32.30 | 9.625 | 244.48 | 0.312 | 7.92 | PS | — | — | — | — | — | — | — |
36.00 | 9.625 | 244.48 | 0.352 | 8.94 | PS | PSLB | PSLB | — | — | — | — | — | |
40.00 | 9.625 | 244.48 | 0.395 | 10.03 | — | PSLB | PSLB | PLB | PLB | PLB | — | — | |
43.50 | 9.625 | 244.48 | 0.435 | 11.05 | — | — | PLB | PLB | PLB | PLB | PLB | — | |
47.00 | 9.625 | 244.48 | 0.472 | 11.99 | — | — | PLB | PLB | PLB | PLB | PLB | PLB | |
53.50 | 9.625 | 244.48 | 0.545 | 13.84 | — | — | — | PLB | PLB | PLB | PLB | PLB | |
58.40 | 9.625 | 244.48 | 0.595 | 15.11 | — | — | — | PLB | PLB | PLB | PLB | PLB | |
59.40 | 9.625 | 244.48 | 0.609 | 15.47 | — | — | — | — | — | P | — | — | |
64.90 | 9.625 | 244.48 | 0.672 | 17.07 | — | — | — | — | — | P | — | — | |
70.30 | 9.625 | 244.48 | 0.734 | 18.64 | — | — | — | — | — | P | — | — | |
75.60 | 9.625 | 244.48 | 0.797 | 20.24 | — | — | — | — | — | P | — | — |
OCTG Casing Pipe Size API5CT | Weight Lb/ft | Outside Diameter | Wall Thickness | Type End Finish | |||||||||
Grade | |||||||||||||
ln. | mm | ln. | mm | H-40 | J-55 K-55 | M-65 | L-80 C-95 | N-80 | C-90T-95 | P-110 | Q-125 | ||
10 3/4” | 32.75 | 10.75 | 273.05 | 0.279 | 7.09 | PS | — | — | — | — | — | — | — |
40.50 | 10.75 | 273.05 | 0.350 | 8.89 | PS | PSB | PSB | — | — | — | — | — | |
45.50 | 10.75 | 273.05 | 0.400 | 10.16 | — | PSB | PSB | — | — | — | — | — | |
51.00 | 10.75 | 273.05 | 0.450 | 11.43 | — | PSB | PSB | PSB | PSB | PSB | PSB | — | |
55.50 | 10.75 | 273.05 | 0.495 | 12.57 | — | — | PSB | PSB | PSB | PSB | PSB | — | |
60.70 | 10.75 | 273.05 | 0.545 | 13.84 | — | — | — | — | — | PSB | PSB | PSB | |
65.70 | 10.75 | 273.05 | 0.595 | 15.11 | — | — | — | — | — | PSB | PSB | PSB | |
73.20 | 10.75 | 273.05 | 0.672 | 17.07 | — | — | — | — | — | P | — | — | |
79.20 | 10.75 | 273.05 | 0.734 | 18.64 | — | — | — | — | — | P | — | — | |
85.30 | 10.75 | 273.05 | 0.797 | 20.24 | — | — | — | — | — | P | — | — | |
11 3/4” | 42.00 | 11.75 | 298.45 | 0.333 | 8.46 | PS | — | — | — | — | — | — | — |
47.00 | 11.75 | 298.45 | 0.375 | 9.53 | — | PSB | PSB | — | — | — | — | — | |
54.00 | 11.75 | 298.45 | 0.435 | 11.05 | — | PSB | PSB | — | — | — | — | — | |
60.00 | 11.75 | 298.45 | 0.489 | 12.42 | — | PSB | PSB | PSB | PSB | PSB | PSB | PSB | |
65.00 | 11.75 | 298.45 | 0.534 | 13.56 | — | — | — | P | P | P | P | P | |
71.00 | 11.75 | 298.45 | 0.582 | 14.78 | — | — | — | P | P | P | P | P | |
13 3/8” | 48.00 | 13.375 | 339.73 | 0.330 | 8.38 | PS | — | — | — | — | — | — | — |
54.50 | 13.375 | 339.73 | 0.380 | 9.65 | — | PSB | PSB | — | — | — | — | — | |
61.00 | 13.375 | 339.73 | 0.430 | 10.92 | — | PSB | PSB | — | — | — | — | — | |
68.00 | 13.375 | 339.73 | 0.480 | 12.19 | — | PSB | PSB | PSB | PSB | PSB | PSB | — | |
72.00 | 13.375 | 339.73 | 0.514 | 13.06 | — | — | — | PSB | PSB | PSB | PSB | PSB | |
P-plain end; S-short round thread; L-long round thread; B-buttress thread |
OCTG TUBING PIPE SIZES
Note: P = plain end, N = Non-upset thread and coupling, U = upset thread and coupling. Sizes per API 5CT specification
Source: API – American Petroleum Institute
OCTG Pipe Sizes (Tubing) API5CT | Weight Lb/ft | Outside Diameter | Wall Thickness | Nominal Weight | Type End Finish | |||||||
Grade | ||||||||||||
Nonupset | Ex-upset | mm | mm | Nonupset | Ex-upset | J-55 | L-80 | N-80 | C-90 | T-95 | P-110 | |
T & C | T & C | T & C | T & C | |||||||||
2 3/8” | 4 | — | 60.32 | 4.24 | 5.95 | — | PN | PN | PN | PN | PN | — |
4.6 | 4.7 | 60.32 | 4.83 | 6.85 | 6.99 | PNU | PNU | PNU | PNU | PNU | PNU | |
5.8 | 5.95 | 60.32 | 6.45 | 8.63 | 8.85 | — | PNU | PNU | PNU | PNU | PNU | |
6.6 | — | 60.32 | 7.49 | 9.82 | — | — | P | — | P | P | — | |
7.35 | 7.45 | 60.32 | 8.53 | 10.94 | 11.09 | — | PU | — | PU | PU | — | |
2 7/8” | 6.4 | 6.5 | 73.02 | 5.51 | 9.52 | 9.67 | PUN | PNU | PNU | PNU | PNU | PNU |
7.8 | 7.9 | 73.02 | 7.01 | 11.61 | 11.76 | — | PNU | PNU | PNU | PNU | PNU | |
8.6 | 8.7 | 73.02 | 7.82 | 12.8 | 12.95 | — | PNU | PNU | PNU | PNU | PNU | |
9.35 | 9.45 | 73.02 | 8.64 | 13.91 | 14.06 | — | PU | — | PU | PU | — | |
10.5 | — | 73.02 | 9.96 | 15.63 | — | — | P | — | P | P | — | |
11.5 | — | 73.02 | 11.18 | 17.11 | — | — | P | — | P | P | — | |
3 1/2” | 7.7 | — | 88.9 | 5.49 | 11.46 | — | PN | PN | PN | PN | PN | — |
9.2 | 9.3 | 88.9 | 6.45 | 13.69 | 13.84 | PNU | PNU | PNU | PNU | PNU | PNU | |
10.2 | — | 88.9 | 7.34 | 15.18 | — | PN | PN | PN | PN | PN | — | |
12.7 | 12.95 | 88.9 | 9.52 | 18.9 | 19.27 | — | PNU | PNU | PNU | PNU | PNU | |
14.3 | — | 88.9 | 10.92 | 21.28 | — | — | P | — | P | P | — | |
15.5 | — | 88.9 | 12.09 | 23.07 | — | — | P | — | P | P | — | |
17 | — | 88.9 | 13.46 | 25.3 | — | — | P | — | P | P | — | |
4” | 9.5 | — | 101.6 | 5.74 | 14.14 | — | PN | PN | PN | PN | PN | PN |
10.7 | 11 | 101.6 | 6.65 | — | 16.37 | PU | PU | PU | PU | PU | PU | |
13.2 | — | 101.6 | 8.38 | 19.64 | — | — | P | — | P | P | — | |
16.1 | — | 101.6 | 10.54 | 23.96 | — | — | P | — | P | P | — | |
18.9 | — | 101.6 | 12.7 | 28.13 | — | — | P | — | P | P | — | |
22.2 | — | 101.6 | 15.49 | 33.04 | — | — | P | — | P | P | — | |
4 1/2” | 12.6 | 12.75 | 114.3 | 6.88 | 18.75 | 18.97 | PUN | PNU | PNU | PNU | PNU | PNU |
15.2 | — | 114.3 | 8.56 | 22.62 | — | — | P | — | P | P | — | |
17 | — | 114.3 | 9.65 | 25.3 | — | — | P | — | P | P | — | |
18.9 | — | 114.3 | 10.92 | 28.13 | — | — | P | — | P | P | — | |
21.5 | — | 114.3 | 12.7 | 32 | — | — | P | — | P | P | — | |
23.7 | — | 114.3 | 14.22 | 35.27 | — | — | P | — | P | P | — | |
26.1 | — | 114.3 | 16 | 38.84 | — | — | P | — | P | P | — |
API 5CT TOLERANCES FOR OCTG PIPES
Execution | Outer Diameter | Wall Thickness |
Cold rolled | Tube sizes(mm) | Tolerances(mm) |
<114.3 | ±0.79 | -12.5% |
≥114.3 | -0.5%,+1% |
MATERIALS FOR OCTG PIPES
The most common materials for OCTG pipes are API H40, J55, K55, L80, N80, P110, and Q125 (casing and tubing pipes). These API grades feature increasing mechanical properties (tensile and yield strength).
OCTG casing and tubing pipes are available in the following material grades:
API H40
API H40 grade is for general-purpose OCTG pipe material with the following mechanical properties:
Chemical Composition
C | Mn | Mo | Cr | Ni | Cu | Ti | P | S | Si | V | Al | |
---|---|---|---|---|---|---|---|---|---|---|---|---|
Min | – | – | – | – | – | – | – | – | – | – | – | – |
Max | – | – | – | – | – | – | – | 0.030 | 0.030 | – | – | – |
Mechanical Properties
Min Tensile Strength | 414 MPa | 60,000 psi min |
Min Yield Strength | 276 MPa | 552 MPa max |
40,000 psi | 80,000 psi max | |
Total Elongation Under Load | 0.500 % | – |
API J55
The J55 API-5CT casing pipe is a comparatively low steel grade in oil drilling. It is widely applied to shallow oil and gas extraction. Because of its low cost among other grades of steel, it enjoys wider applications and can be generally used in shallow wells, geothermal wells, and water wells.
Chemical Composition
C | Mn | Mo | Cr | Ni | Cu | Ti | P | S | Si | V | Al | |
---|---|---|---|---|---|---|---|---|---|---|---|---|
Min | – | – | – | – | – | – | – | – | – | – | – | – |
Max | – | – | – | – | – | – | – | 0.030 | 0.030 | – | – | – |
Mechanical Properties
Min Tensile Strength | 517 MPa | 75,000 psi min |
Min Yield Strength | 379 MPa | 552 MPa max |
55,000 psi | 80,000 psi max | |
Total Elongation Under Load | 0.500 % | – |
API L80
L80 belongs to the steel grade group of corrosion-resistant casing. L80 API oilfield casing pipe includes L80-1, L80-9Cr, and L80-13Cr. L80-1 is used in the H2S environment, while L80-9Cr and L80-13Cr are used in the CO2 environment. In the corrosive environment in which carbon dioxide predominates, Super 13Cr has a higher corrosion resistance than L80-13Cr. With a relatively high price, the product applies to more complicated geological conditions and runs down deeper into the well. In the exploitation of oil and gas, the use of L80 is less frequent than J55, N80, and other materials.
Chemical Composition
C | Mn | Mo | Cr | Ni | Cu | Ti | P | S | Si | V | Al | |
---|---|---|---|---|---|---|---|---|---|---|---|---|
Min | – | – | – | – | – | – | – | – | – | – | – | – |
Max | 0.430 | 1.900 | – | – | 0.250 | 0.350 | – | 0.030 | 0.030 | 0.450 | – | – |
Mechanical Properties
Min Tensile Strength | 655 MPa | 95,000 psi min |
Min Yield Strength | 552 MPa | 655 MPa max |
80,000 psi | 95,000 psi max | |
Total Elongation Under Load | 0.500 % | – |
Hardness | 23 Max HRC | 241 Max HBW |
9Cr-L80 Chemical Composition
C | Mn | Mo | Cr | Ni | Cu | Ti | P | S | Si | V | Al | |
---|---|---|---|---|---|---|---|---|---|---|---|---|
Min | – | 0.300 | 0.900 | 8.000 | – | – | – | – | – | – | – | – |
Max | 0.150 | 0.600 | 1.100 | 10.000 | 0.500 | 0.250 | – | 0.020 | 0.010 | 1.000 | – | – |
9Cr-L80 Mechanical Properties
Min Tensile Strength | 655 MPa | 95,000 psi min |
Min Yield Strength | 552 MPa | 655 MPa max |
80,000 psi | 95,000 psi max | |
Total Elongation Under Load | 0.500 % | – |
Hardness | 23 Max HRC | 241 Max HBW |
API N80
API-5CT N80 oilfield casing pipe contains N80-1 and N80-Q types. Those two materials are absolutely consistent regarding the chemical composition and mechanical attributes, they are just variations in the heat treatment.
During the heat treatment, N80-1 steel is treated by normalizing and tempering, while N80Q steel is treated by quenching and tempering. Therefore, the collapsing strength and internal pressure strength of N80Q are higher than that of N80-1. N80-1 or N80Q should be clearly shown by the designer when the N80 casing is selected.
Due to the high capability of the N80 material, those API-5CT casing pipes are broadly applied in natural gas as well as coal bed methane extraction, and geothermal wells.
Chemical Composition
C | Mn | Mo | Cr | Ni | Cu | Ti | P | S | Si | V | Al | |
---|---|---|---|---|---|---|---|---|---|---|---|---|
Min | – | – | – | – | – | – | – | – | – | – | – | – |
Max | – | – | – | – | – | – | – | 0.030 | 0.030 | – | – | – |
Mechanical Properties
Min Tensile Strength | 689 MPa | 100,000 psi min |
Min Yield Strength | 552 MPa | 758 MPa max |
80,000 psi | 110,000 psi max | |
Total Elongation Under Load | 0.500 % | – |
Hardness | – | – |
API P110
The P110 API-5CT steel casing pipe is the high grade amongst other grades of steel. The white band is marked on the finished casing to point out the materials. During petroleum drilling and production, this pipe is generally used in a variety of complicated territories due to its higher tensile strength and higher yield. It goes down the deepest into the well among other types.
However, the price is comparatively high, as well as the quantity of usage is comparatively few. P110 casing pipe is mainly used in a particular surrounding and when the drilling depth extends to a particular level.
API Q125
This API grade is generally used for deep wellbore service and not in sour condensate wells. The hardness testing (quadrant) is required without any specified limits other than the variation between readings.
API5CT MATERIALS CHEMICAL COMPOSITION
Group | OCTG pipe materials | Type | C | Mn | Mo | Cr | Ni max. | Cu max. | P max. | S max. | Si max. | ||||
---|---|---|---|---|---|---|---|---|---|---|---|---|---|---|---|
min. | max. | min. | max. | min. | max. | min. | max. | ||||||||
1 | 2 | 3 | 4 | 5 | 6 | 7 | 8 | 9 | 10 | 11 | 12 | 13 | 14 | 15 | 16 |
1 | H40 | – | – | – | – | – | – | – | – | – | – | – | 0.03 | 0.03 | – |
J55 | – | – | – | – | – | – | – | – | – | – | – | 0.03 | 0.03 | – | |
K55 | – | – | – | – | – | – | – | – | – | – | – | 0.03 | 0.03 | – | |
N80 | 1 | – | – | – | – | – | – | – | – | – | – | 0.03 | 0.03 | – | |
N80 | Q | – | – | – | – | – | – | – | – | – | – | 0.03 | 0.03 | – | |
R95 | – | – | 0.45 c | – | 1.9 | – | – | – | – | – | – | 0.03 | 0.03 | 0.45 | |
2 | M65 | – | – | – | – | – | – | – | – | – | – | – | 0.03 | 0.03 | – |
L80 | 1 | – | 0.43 a | – | 1.9 | – | – | – | – | 0.25 | 0.35 | 0.03 | 0.03 | 0.45 | |
L80 | 9Cr | – | 0.15 | 0.3 | 0.6 | 0.9 | 1.1 | 8 | 10 | 0.5 | 0.25 | 0.02 | 0.01 | 1 | |
L80 | 13Cr | 0.15 | 0.22 | 0.25 | 1 | – | – | 12 | 14 | 0.5 | 0.25 | 0.02 | 0.01 | 1 | |
C90 | 1 | – | 0.35 | – | 1.2 | 0.25 b | 0.85 | – | 1.5 | 0.99 | – | 0.02 | 0.01 | – | |
T95 | 1 | – | 0.35 | – | 1.2 | 0.25 d | 0.85 | 0.4 | 1.5 | 0.99 | – | 0.02 | 0.01 | – | |
C110 | – | – | 0.35 | – | 1.2 | 0.25 | 1 | 0.4 | 1.5 | 0.99 | – | 0.02 | 0.005 | – | |
3 | P110 | e | – | – | – | – | – | – | – | – | – | – | 0.030 e | 0.030 e | – |
4 | Q125 | 1 | – | 0.35 | 1.35 | – | 0.85 | – | 1.5 | 0.99 | – | 0.02 | 0.01 | – |
a The carbon content for L80 may be increased up to 0.50 % maximum if the product is oil-quenched.
b The molybdenum content for Grade C90 Type 1 has no minimum tolerance if the wall thickness is less than 17.78 mm.
c The carbon content for R95 may be increased up to 0.55 % maximum if the product is oil-quenched.
d The molybdenum content for T95 Type 1 may be decreased to 0.15 % minimum if the wall thickness is less than 17.78 mm.
e For EW Grade P110, the phosphorus content shall be 0.020 % maximum and the sulfur content 0.010 % maximum.
NL = no limit. Elements shown shall be reported in product analysis.
OCTG PIPE MATERIALS – MECHANICAL PROPERTIES
Group | OCTG pipe materials | Type | Total elongation under load % | Yield strength MPa | Tensile strength min. MPa | Hardness a max. | Specified wall thickness mm | Allowable hardness variation b HRC | ||
---|---|---|---|---|---|---|---|---|---|---|
min. | max . | HRC | HBW | |||||||
1 | 2 | 3 | 4 | 5 | 6 | 7 | 8 | 9 | 10 | 11 |
1 | H40 | – | 0.5 | 276 | 552 | 414 | – | – | – | – |
J55 | – | 0.5 | 379 | 552 | 517 | – | – | – | – | |
K55 | – | 0.5 | 379 | 552 | 655 | – | – | – | – | |
N80 | 1 | 0.5 | 552 | 758 | 689 | – | – | – | – | |
N80 | Q | 0.5 | 552 | 758 | 689 | – | – | – | – | |
R95 | – | 0.5 | 655 | 758 | 724 | – | – | – | – | |
2 | M65 | – | 0.5 | 448 | 586 | 586 | 22 | 235 | – | – |
L80 | 1 | 0.5 | 552 | 655 | 655 | 23 | 241 | – | – | |
L80 | 9Cr | 0.5 | 552 | 655 | 655 | 23 | 241 | – | – | |
L80 | 13Cr | 0.5 | 552 | 655 | 655 | 23 | 241 | – | – | |
C90 | 1 | 0.5 | 621 | 724 | 689 | 25.4 | 255 | ≤ 12.70 12.71 to 19.04 19.05 to 25.39 ≥ 25.40 | 3.0 4.0 5.0 6.0 | |
T95 | 1 | 0.5 | 655 | 758 | 724 | 25.4 | 255 | ≤ 12.70 12.71 to 19.04 19.05 to 25.39 ≥ 25.40 | 3.0 4.0 5.0 6.0 | |
C110 | – | 0.7 | 758 | 828 | 793 | 30 | 286 | ≤ 12.70 12.71 to 19.04 19.05 to 25.39. ≥ 25.40 | 3.0 4.0 5.0 6.0 | |
3 | P110 | – | 0.6 | 758 | 965 | 862 | – | – | – | – |
4 | Q125 | 1 | 0.65 | 862 | 1034 | 931 | b | – | ≤ 12.70 12.71 to 19.04 ≥ 19.05 | 3.0 4.0 5.0 |
a In case of dispute, laboratory Rockwell C hardness testing shall be used as the referee method. b No hardness limits are specified, but the maximum variation is restricted as a manufacturing control in accordance with 7.8 and 7.9 of API Spec. 5CT. |
Conclusion
OCTG (Oil Country Tubular Goods) pipes play a vital role in the oil and gas industry due to their importance in various stages of exploration, drilling, production, and transportation of hydrocarbons. Here are some key reasons why OCTG pipes are crucial in the oil and gas sector:
- Oil & Gas Well Construction and Integrity:
- OCTG pipes are essential for constructing oil and gas wells, providing structural support, and maintaining the integrity of the wellbore.
- Casing pipes are used to line the wellbore and prevent collapse, ensuring the stability of the hole and protecting the surrounding formations from damage.
- Tubing pipes are inserted inside the casing to convey oil, natural gas, and production fluids from the reservoir to the surface, while also supporting downhole equipment such as pumps and packers.
- Fluid Conveyance and Production:
- OCTG pipes serve as conduits for the transmission of drilling fluid during the drilling process, allowing for the removal of rock cuttings and debris from the wellbore to the surface.
- Tubing pipes facilitate the production of oil and gas by providing a pathway for the flow of hydrocarbons from the reservoir to the surface production facilities.
- Drill pipes transmit drilling torque and axial loads to the drill bit, enabling the penetration of the earth’s subsurface layers and the extraction of oil and gas reserves.
- Oil & Gas Well Completion and Intervention:
- OCTG pipes are used in well completion and intervention operations to install downhole equipment such as casing hangers, packers, and production tubing.
- Coiled tubing, a type of OCTG product, is employed for well intervention tasks such as acidizing, fracturing, and well cleanout operations to enhance production and reservoir performance.
- Corrosion Protection and Environmental Safety:
- OCTG pipes are designed to withstand harsh downhole conditions, including high pressure, temperature, and corrosive environments encountered in oil and gas wells.
- Protective coatings and corrosion inhibitors are applied to OCTG pipes to enhance their corrosion resistance and extend their service life, ensuring the integrity and safety of the wellbore and surrounding environment.
- Industry Standards and Regulations Compliance:
- OCTG pipes must meet stringent industry standards and regulatory requirements set by organizations such as the American Petroleum Institute (API) and international standards organizations.
- Compliance with industry standards ensures the quality, reliability, and compatibility of OCTG pipes with drilling equipment and procedures, as well as environmental and safety regulations.
In summary, OCTG pipes are indispensable components in the oil and gas industry, providing critical support and functionality throughout the lifecycle of oil and gas wells. From exploration and drilling to production and intervention, OCTG pipes contribute to the efficient and safe extraction of hydrocarbon reserves, driving the global energy supply chain and supporting economic growth and development worldwide.
7 Responses
It is nice to read this article. I would like to have specs of the PH6 tubing if you have. As I searched the internet but didn’t found. please contact me on my email info@drillingmanual.com
Hello. I would like to know which of these casings would be best suited to be used in a percussion application where the casings would be driven from ground level using a high speed air hammer.
Also we have had problems when threading casing with chrome. When screwing casing together these joints will then not unscrew. Can you explain.
Please advise
Bobby
Do you have tubing pipes of the sizes 4′ 4 5/8′, and 5′ for sale. It must be buttress threaded and with a threaded coupling joints with the following specs:
L: around 32″
Conditions : tested and galvanized, used , new
thickness: above 0.23 mm
quantity : open
The J55 API -5CT casing pipe is a comparatively low steel grade in oil drilling. It is widely applied to shallow oil and gas extraction. Because of its low cost among other grades of steel, it enjoys wider applications, can be generally used in shallow wells, geothermal wells, and water wells.
Thank you for your appreciated comment. Should you need further information on some specific topics, kindly send us an email to support@projectmaterials.com. To submit an RFQ for piping materials, please visit this page: https://projectmaterials.com/submit-rfq-mto. Best regards, Projectmaterials
It is good article for me.
We are drilling and cementing tools supplier.
Thank you for your appreciated comment. Should you need further information on some specific topics, kindly send us an email to support@projectmaterials.com. To submit an RFQ for piping materials, please visit this page: https://projectmaterials.com/submit-rfq-mto. Best regards, Projectmaterials