Ductile iron pipes are robust and versatile, known for their strength and durability. Their unique microstructure of spherical-shaped graphite obtained by adding magnesium or cerium to molten iron, allows them to bend without breaking. These pipes are ideal for various applications, including water and wastewater, gas distribution, and industrial processes. They come with protective linings and coatings to combat corrosion and ensure water quality and are both long-lasting and recyclable. The article delves into the features and applications of this special type of pipes.
DUCTILE IRON PIPES
WHAT ARE DUCTILE IRON PIPES
Ductile iron pipes, known for their remarkable combination of strength, durability, and flexibility, are a modern innovation in the field of piping materials.
Made from ductile cast iron, these pipes are characterized by their high tensile strength and the ability to withstand significant internal and external pressures, making them an ideal choice for water and wastewater systems, gas distribution, and industrial applications.
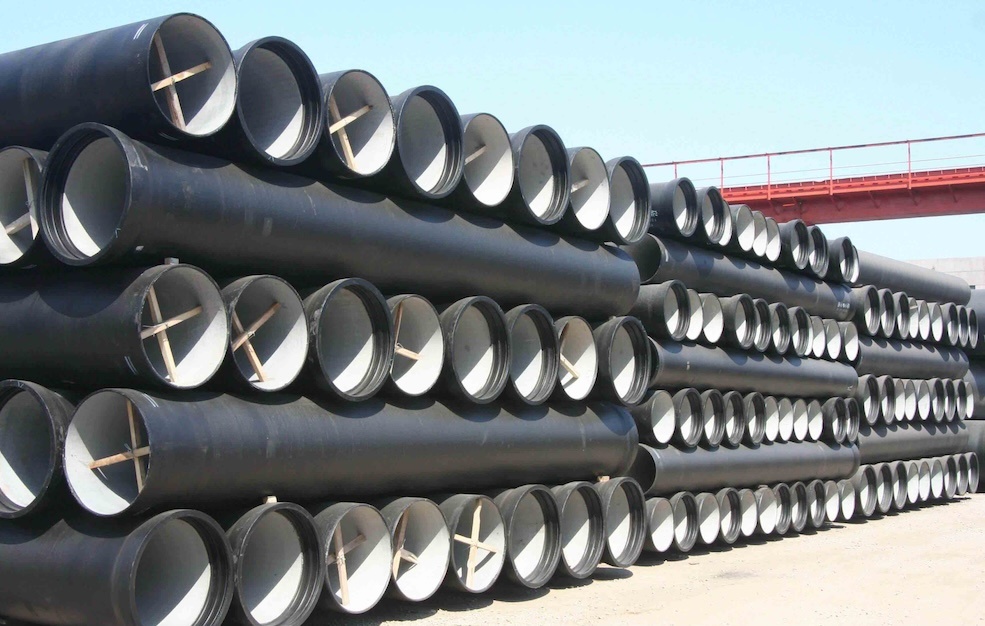
Ductile iron pipes are manufactured using centrifugal casting techniques, followed by annealing processes to enhance their mechanical properties further. They are available in a variety of sizes and lengths, with internal linings and external coatings such as cement mortar, zinc, and asphalt to improve corrosion resistance and water quality. The joint designs of ductile iron pipes allow for easy assembly and flexibility in the field, accommodating a range of laying conditions and making them a preferred choice for modern infrastructure projects. Their longevity, combined with their recyclability, also aligns with sustainable development goals, making ductile iron pipes a resilient and environmentally friendly option for piping systems.
WHAT IS DUCTILE IRON
Ductile iron, also known as nodular cast iron or spheroidal graphite iron, is a type of cast iron characterized by its high strength and ductility.
Its unique microstructure, which contains nodular graphite inclusions within a ferritic or pearlitic matrix, is the result of adding magnesium or cerium to molten iron. This spherical graphite structure imparts exceptional mechanical properties to the ductile iron, notably its ability to bend without breaking, unlike the brittle nature of traditional cast iron.
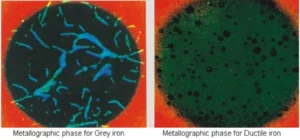
APPLICATIONS OF DUCTILE IRON PIPES
Ductile iron pipes are utilized in a broad range of applications, owing to their robustness and flexibility:
- Water Supply and Distribution: Their excellent pressure and impact resistance makes them ideal for water mains, distribution lines, and pumping stations.
- Sewer and Wastewater Systems: Ductile iron pipes are used in gravity and pressure sewer systems, offering high resistance to wear and corrosion from sewage.
- Gas Distribution: Their strength and joint integrity make them suitable for the safe transport of natural gas.
- Industrial Applications: Used in process piping systems for conveying liquids, gases, and slurries in various industrial sectors.
Due to these undeniable benefits, ductile iron pipes have solidified their position in the infrastructure of modern societies due to their unmatched combination of strength, ductility, and longevity. Their adaptability across a spectrum of applications, from municipal water systems to industrial processes, underscores their significance.
ADVANTAGES/DISADVANTAGES OF DUCTILE IRON PIPES
Advantages
Ductile iron pipes are robust and efficient solutions for the applications mentioned above. They feature:
- Strength and Durability: Ductile iron pipes possess high tensile strength and the ability to withstand significant internal and external pressures, reducing the risk of cracks and failures.
- Flexibility and Impact Resistance: Unlike rigid pipe materials, ductile iron can flex under loads, making it more resistant to impact and less likely to break during installation or due to ground movement.
- Corrosion Resistance: With proper coatings and linings, ductile iron pipes offer excellent resistance to corrosion, extending their service life.
- Ease of Installation: The use of push-on or mechanical joints allows for quick and reliable installation, reducing project timelines and costs.
- Sustainability: Ductile iron pipes can be recycled at the end of their service life, contributing to environmental sustainability.
Disadvantages
While ductile iron pipes offer numerous benefits, certain considerations must be taken into account:
- Corrosion Protection: Depending on the soil and water characteristics, additional protective measures, such as polyethylene encasement, may be required to prevent corrosion.
- Weight: Ductile iron pipes are heavier than some alternative materials, which can impact handling and installation costs.
- Regular Inspection: Routine inspections and maintenance are necessary to ensure the integrity and performance of ductile iron piping systems over time.
MANUFACTURING PROCESS
The production of ductile iron pipes involves several key steps:
- Melting and Treatment: The process begins with the melting of iron, along with scrap steel and additives, in a furnace. The molten iron is then treated with magnesium (or cerium) to alter the graphite structure from flakes to spheroids, enhancing the iron’s ductility.
- Casting: The treated molten iron is cast into molds of the desired pipe sizes and shapes. Most ductile iron pipes are manufactured using centrifugal casting methods, where the molten iron is poured into rotating molds to create pipes with uniform thickness and high density.
- Annealing: After casting, the pipes undergo annealing, a heat treatment process that further improves ductility and relieves internal stresses.
- Finishing: The pipes are then cooled, cleaned, and subjected to various finishing processes, including zinc coating, asphalt lining, or cement-mortar lining to enhance corrosion resistance and improve water quality.
The production process is shown in this video (Source: McWane Ductile)
DUCTILE IRON PIPE DIMENSIONS
Ductile iron pipes, widely used for their durability and strength, are manufactured according to various specifications, including American and European standards. These standards provide guidelines on dimensions, thicknesses, and other critical attributes to ensure the pipes meet the required performance and quality levels for different applications. Below are the key dimensions and thicknesses according to American (ANSI/AWWA) and European (EN) specs.
AMERICAN SPECS (ANSI/AWWA C151)
OD/ID, WT/Class
The American Water Works Association (AWWA) provides specifications for ductile iron pipes through ANSI/AWWA C151/A21.51. These specifications cover a range of diameters and pressure classes:
- Diameter: The nominal sizes for ductile iron pipes under AWWA standards range from 3 inches (about 76 mm) to 64 inches (about 1,626 mm).
- Thickness Class: AWWA standards specify thickness classes rather than specific wall thicknesses. These classes are designated as Class 50 through Class 56 for pipes up to 24 inches in diameter, with each class corresponding to a different wall thickness designed to withstand varying levels of internal pressure and external loads.
- Pressure Class: The pipes are also categorized by pressure classes, typically ranging from 150 psi (about 1,034 kPa) to 350 psi (about 2,413 kPa), indicating the maximum operating pressure the pipes are designed to handle.
- Inside Diameter (UNL/CL/DCL): Inside diameter varies depending on the presence of internal lining material (UNL = unlined pipe, i.e. bare ductile iron, CL = cement lined, DCL = Double cement lined)
Note that:
- ANSI/AWWA C151/A21.51: American standard for ductile iron pipes for water and other liquids.
- ANSI/AWWA C115/A21.15: For flanged ductile iron pipes.
Here is a size chart with the dimensions and weights of ductile iron pipes for water transmission (NPS 3″ to 54″ – Class 53, the most commonly used for water applications):
NPS | NPS mm | OD inch. | OD mm | Class | WT inch. | Weight in Lb/ft | Weight with Water Lb/ft |
---|---|---|---|---|---|---|---|
3″ | 80.00 | 3.96 | 100.60 | 53.00 | 0.31 | 11.20 | 15.00 |
4″ | 100.00 | 4.80 | 121.90 | 53.00 | 0.32 | 14.20 | 20.10 |
6″ | 150.00 | 6.90 | 175.30 | 53.00 | 0.34 | 22.00 | 35.10 |
8″ | 200.00 | 9.05 | 229.90 | 53.00 | 0.36 | 31.00 | 54.00 |
10″ | 250.00 | 11.10 | 281.90 | 53.00 | 0.38 | 40.40 | 76.80 |
12″ | 300.00 | 13.20 | 335.20 | 53.00 | 0.40 | 50.70 | 103.00 |
14″ | 350.00 | 15.30 | 388.60 | 53.00 | 0.42 | 62.40 | 133.50 |
16″ | 400.00 | 17.40 | 442.00 | 53.00 | 0.43 | 72.80 | 165.90 |
18″ | 450.00 | 19.50 | 495.30 | 53.00 | 0.44 | 83.60 | 201.50 |
20″ | 500.00 | 21.60 | 548.60 | 53.00 | 0.45 | 95.20 | 241.00 |
24″ | 600.00 | 25.80 | 655.30 | 53.00 | 0.47 | 119.20 | 329.40 |
30″ | 750.00 | 32.00 | 812.80 | 53.00 | 0.51 | 161.30 | 487.80 |
36″ | 900.00 | 38.30 | 972.80 | 53.00 | 0.58 | 219.50 | 688.80 |
42″ | 1050.00 | 44.50 | 1130.30 | 53.00 | 0.65 | 285.20 | 920.10 |
48″ | 1200.00 | 50.80 | 1290.30 | 53.00 | 0.72 | 360.30 | 1189.20 |
54″ | 1350.00 | 57.10 | 1450.30 | 53.00 | 0.81 | 455.00 | 1502.20 |
Pipe Lengths (ANSI/AWWA)
Under the American National Standards Institute (ANSI) and the American Water Works Association (AWWA) specifications, particularly ANSI/AWWA C151/A21.51, ductile iron pipes are commonly provided in the following lengths:
- Laying Lengths: The standard laying length for ductile iron pipes in the United States is usually 18 feet (about 5.5 meters) or 20 feet (about 6.1 meters) for the main body of the pipe, not including the length of the joint or bell.
- Custom Lengths: Some projects may require pipes of specific lengths to accommodate unique design considerations, and manufacturers can provide pipes in custom lengths according to project specifications.
EUROPEAN SPECS (EN 545/598)
OD/ID, WT/Class
The European Standard EN 545 and EN 598 govern the dimensions and thicknesses of ductile iron pipes for water and wastewater applications, respectively:
- Diameter: EN standards cover a wide range of nominal diameters, from DN 40 (about 40 mm) to DN 2000 (about 2,000 mm).
- Wall Thickness: Unlike the AWWA standards, EN standards provide specific wall thicknesses for each diameter and class of pipe. The wall thickness is determined based on the pipe’s nominal diameter and its class designation, which corresponds to the pipe’s designed operating pressure and application environment.
- Class Designation: EN 545 and EN 598 classify pipes by their allowable operating pressures and application environments. For example, standard pressure classes include C40, C30, and C25, where the number represents the nominal pressure in bars (e.g., C40 for 40 bars).
DN | OD (mm/inch.) | Pipe WT (mm/inch.) | ||
Class 40 | K9 | K10 | ||
40 | 56 (2.205) | 4.8 (0.189) | 6.0 (0.236) | 6.0 (0.236) |
50 | 66 (2.598) | 4.8 (0.189) | 6.0 (0.236) | 6.0 (0.236) |
60 | 77 (3.031) | 4.8 (0.189) | 6.0 (0.236) | 6.0 (0.236) |
65 | 82 (3.228) | 4.8 (0.189) | 6.0 (0.236) | 6.0 (0.236) |
80 | 98 (3.858) | 4.8 (0.189) | 6.0 (0.236) | 6.0 (0.236) |
100 | 118 (4.646) | 4.8 (0.189) | 6.0 (0.236) | 6.0 (0.236) |
125 | 144 (5.669) | 4.8 (0.189) | 6.0 (0.236) | 6.0 (0.236) |
150 | 170 (6.693) | 5.0 (0.197) | 6.0 (0.236) | 6.5 (0.256) |
200 | 222 (8.740) | 5.4 (0.213) | 6.3 (0.248) | 7.0 (0.276) |
250 | 274 (10.787) | 5.8 (0.228) | 6.8 (0.268) | 7.5 (0.295) |
300 | 326 (12.835) | 6.2 (0.244) | 7.2 (0.283) | 8.0 (0.315) |
350 | 378 (14.882) | 7.0 (0.276) | 7.7 (0.303) | 8.5 (0.335) |
400 | 429 (16.890) | 7.8 (0.307) | 8.1 (0.319) | 9.0 (0.354) |
450 | 480 (18.898) | – | 8.6 (0.339) | 9.5 (0.374) |
500 | 532 (20.945) | – | 9.0 (0.354) | 10.0 (0.394) |
600 | 635 (25.000) | – | 9.9 (0.390) | 11.1 (0.437) |
700 | 738 (29.055) | – | 10.9 (0.429) | 12.0 (0.472) |
800 | 842 (33.150) | – | 11.7 (0.461) | 13.0 (0.512) |
900 | 945 (37.205) | – | 12.9 (0.508) | 14.1 (0.555) |
1000 | 1,048 (41.260) | – | 13.5 (0.531) | 15.0 (0.591) |
1100 | 1,152 (45.354) | – | 14.4 (0.567) | 16.0 (0.630) |
1200 | 1,255 (49.409) | – | 15.3 (0.602) | 17.0 (0.669) |
1400 | 1,462 (57.559) | – | 17.1 (0.673) | 19.0 (0.748) |
1500 | 1,565 (61.614) | – | 18.0 (0.709) | 20.0 (0.787) |
1600 | 1,668 (65.669) | – | 18.9 (0.744) | 51.0 (2.008) |
1800 | 1,875 (73.819) | – | 20.7 (0.815) | 23.0 (0.906) |
2000 | 2,082 (81.969) | – | 22.5 (0.886) | 25.0 (0.984) |
Both American and European specifications ensure that ductile iron pipes are suitable for their intended applications, providing essential guidelines for manufacturers and engineers in designing and selecting piping systems. It’s important to consult the latest editions of these standards, as updates and revisions may affect the specifications. Additionally, the choice between American and European standards often depends on regional preferences, project specifications, and local regulatory requirements.
K8, K9, K10 CLASSES (EN 545)
The designations K8, K9, K10, etc., refer to different classes of ductile iron pipes defined primarily by their wall thickness and hence their strength and pressure-handling capabilities. This classification system is widely used in international standards, including ISO 2531 and EN 545, which are commonly referenced for water supply and sewage applications.
These classes are part of the standardized system used to categorize ductile iron pipes based on their nominal wall thickness, which directly correlates with the pipe’s ability to withstand internal pressure.
Understanding K Classes
K Class Number: The “K” value in these designations indicates the class of the pipe, with the number following “K” representing a specific ratio related to the wall thickness. Essentially, the higher the “K” number, the thicker the wall of the pipe and, consequently, the higher its ability to handle pressure.
Pressure Capacity: While the “K” class does not directly specify the pressure rating in bars or psi, it implies a pipe’s durability and strength due to the wall thickness. For instance, K9 pipes are thicker and stronger than K8 pipes, making them suitable for higher-pressure applications.
Calculation: The wall thickness for a given “K” class can be calculated based on the pipe’s internal diameter and the specific “K” value, using formulas provided in the ISO 2531 and EN 545 standards. This calculation ensures that pipes have sufficient strength to handle the expected internal pressures plus a margin for safety.
Common Classes and Applications
- K8: Often used in applications where lower pressures are anticipated or where ground conditions are stable and present minimal risk to the pipe.
- K9: This is the standard class for a wide range of applications, including municipal water supply and distribution networks. It offers a balanced combination of strength and cost-effectiveness.
- K10 and Above: These classes are selected for conditions requiring higher pressure handling or where external loads on the pipe are greater, such as in areas with heavy traffic overhead or unstable ground.
Selection Criteria
Choosing the appropriate “K” class for ductile iron pipes involves considering the operational pressure, the type of fluid being transported, the burial depth of the pipe, soil conditions, and external loads. Engineers also factor in safety, longevity, and compliance with local and international standards when selecting the pipe class.
The “K” classification system provides a standardized approach to specifying the wall thickness and, by extension, the strength and pressure capacity of ductile iron pipes. By selecting the appropriate “K” class, engineers can ensure that piping systems are adequately designed to meet the demands of their intended applications, combining durability with cost efficiency.
Differences between C-Class and K-Class in EN545
The classifications of ductile iron pipes using “C” and “K” values, such as C30, C40, K8, and K9, refer to different standards for defining the pipe’s strength, thickness, and pressure capabilities, primarily within the framework of EN 545, which is a European standard for ductile iron pipes, fittings, accessories, and their joints for water pipelines.
C-Class (C30, C40, etc.)
The “C” classification system specifies the pipe’s nominal pressure class. The number following “C” represents the nominal pressure in bars that the pipe can withstand. For instance:
- C30: Indicates that the pipe is designed to handle a nominal pressure of 30 bars.
- C40: Indicates that the pipe is designed to handle a nominal pressure of 40 bars.
This system directly relates to the pipe’s ability to withstand internal pressures, and it is a straightforward indication of the pipe’s pressure rating. The higher the number, the greater the pressure the pipe can handle. This classification is more directly concerned with the operational pressures within the pipes.
K-Class (K8, K9, etc.)
The “K” classification, on the other hand, is related to the pipe’s wall thickness and indirectly to its pressure capacity. The “K” value is a coefficient used in a formula that determines the wall thickness of the pipe based on its diameter. The formula takes into account the internal pressure, the diameter of the pipe, and the “K” value to calculate the required wall thickness for standard laying conditions. For example:
- K8: A specific “K” class indicating a certain wall thickness ratio, designed for standard pressure applications.
- K9: Typically the standard class for many applications, offering a thicker wall and, hence, capable of withstanding higher internal pressures and external loads compared to K8.
Key Differences and Applications
- Direct vs. Indirect Pressure Indication: The “C” classification directly indicates the pressure rating of the pipe in bars, making it straightforward to determine the pipe’s suitability for specific pressure conditions. The “K” classification indirectly indicates pressure capacity by defining the wall thickness, which correlates with the pipe’s ability to handle both internal pressures and external loads.
- Design Focus: The “C” class is focused on the pipe’s pressure endurance, while the “K” class emphasizes the structural design and thickness, influencing both pressure endurance and physical robustness against external forces.
- Usage: Selection between “C” and “K” classifications will depend on engineering requirements, specific application needs, and local or project-specific standards. The “K” class is often used in specifications for general water supply, whereas the “C” class may be specified when direct pressure requirements are a priority.
Pipe Lengths (EN 545)
European standards, such as EN 545 (for water pipelines) and EN 598 (for sewerage applications), define the lengths of ductile iron pipes as follows:
- Standard Lengths: In Europe, the standard lengths for ductile iron pipes are commonly 6 meters (about 19.7 feet), with a tolerance that can vary slightly depending on the manufacturer’s specifications.
- Short Lengths: For special applications, including fittings and adjustments to the pipeline route, shorter lengths are also available, typically ranging from 1 meter (about 3.3 feet) to 3 meters (about 9.8 feet).
OTHER SPECIFICATIONS FOR DUCTILE IRON PIPES
- International Standard: ISO2531-2009
- UK Standard: BS EN545-2002
- China: GB/T13295-2003
- South Korean Standard: KSD 4311
- Australian Standard: AS 2280
PIPE CONNECTION TYPES
An essential aspect of the ductile iron pipe design and functionality is the type of joints used to connect individual pipe sections.
The joint type affects the ease of installation, the ability to accommodate movement, and, crucially, the long-term integrity of the pipeline. Here are the common types of joints used with ductile iron pipes:
PUSH-ON (TYTON) JOINTS

- Description: Push-on joints, also known as Tyton or slip joints, involve a simple mechanism where the spigot (male end) of one pipe is inserted into the bell (female end) of another with a rubber gasket placed in the bell.
- Advantages: These joints are quick and easy to assemble, require no special tools, and are flexible enough to accommodate slight angular deflections and ground movements.
- Applications: Widely used in water and wastewater systems where moderate pressures are anticipated.
MECHANICAL JOINTS

- Description: Mechanical joints consist of a gland, a gasket, and bolts and nuts. The spigot end of the pipe fits into the bell of the connecting pipe, with the gasket creating a seal and the gland compressing the gasket through the tightening of bolts.
- Advantages: They offer flexibility in alignment and are suitable for applications where disassembly may be required. They can also accommodate slight angular deflections.
- Applications: Suitable for both water and gas distribution systems, especially in areas requiring frequent maintenance or system reconfiguration.
FLANGED JOINTS
- Description: Flanged joints use flanges attached to the ends of pipes, bolted together with a gasket in between to ensure a tight seal.
- Advantages: They provide a rigid and secure connection, allow for easy disassembly, and are ideal for pump connections and fittings where the pipeline connects to equipment.
- Applications: Commonly used in treatment plants, pump stations, and sections of the pipeline that require periodic inspection or maintenance.
RESTRAINED JOINTS

- Description: Restrained joints are designed to prevent separation under axial forces. They can be a variation of push-on or mechanical joints with additional locking mechanisms, such as welded retainer rings or gripping devices.
- Advantages: These joints prevent pipe pullout in applications subject to high internal pressure or external forces, providing a secure connection without the need for thrust blocks.
- Applications: Ideal for sloped terrains, areas subject to flooding, or where the pipeline experiences significant internal pressure fluctuations.
GROOVED/COUPLED JOINTS
- Description: This joint type involves a grooved indentation on the pipe ends, where a coupling is installed to connect the pipes. A rubber gasket within the coupling ensures the seal.
- Advantages: Grooved joints offer rapid assembly and disassembly, flexibility in movement, and can accommodate some angular and linear movement.
- Applications: They are often used in fire protection systems, HVAC, and industrial applications where easy modification of the piping system is a requirement.

MATERIAL GRADES
Ductile iron pipes are available in various material grades, each tailored to meet specific performance criteria and applications. These grades are defined by standards organizations, such as the American Society for Testing and Materials (ASTM), the International Organization for Standardization (ISO), and the European Committee for Standardization (EN).
The differences in material grades typically involve variations in mechanical properties like tensile strength, yield strength, elongation, and hardness, as well as in chemical composition to enhance characteristics like corrosion resistance, durability, and impact resistance. Here are some of the common material grades for ductile iron pipes:
COMMON GRADES
ISO 2531 & EN 545/EN 598 GRADES
- EN-GJS-400-15 (ISO 2531/EN 545): This grade offers excellent ductility with a minimum tensile strength of 400 MPa and is commonly used in water and wastewater applications.
- EN-GJS-450-10 (ISO 2531/EN 545): With a higher tensile strength of 450 MPa, this grade provides a good balance between strength and ductility, suitable for higher-pressure applications.
- EN-GJS-500-7 (ISO 2531/EN 598): This grade is designed for sewage applications, offering increased strength and wear resistance with a minimum tensile strength of 500 MPa.
- EN-GJS-600-3 (ISO 2531/EN 598): The highest strength grade commonly used for ductile iron pipes, with a minimum tensile strength of 600 MPa, suitable for high-pressure and industrial applications.
ASTM A536 GRADES
- 60-40-18: Similar to EN-GJS-400-15, it has a tensile strength of 414 MPa and is known for its outstanding ductility and impact resistance.
- 65-45-12: This grade offers a balance of strength and ductility with a tensile strength of 448 MPa, making it suitable for a variety of applications.
- 80-55-06: With a tensile strength of 552 MPa, this grade is used where higher strength and moderate ductility are required.
- 100-70-03: The highest strength grade in ASTM A536, offering a tensile strength of 689 MPa with lower ductility, is used in applications demanding high strength.
SPECIALTY GRADES
Some manufacturers produce ductile iron pipes in specialty grades that are not explicitly covered by the standard classifications but are designed to offer enhanced properties for specific applications, such as:
- High impact resistance grades: Developed for regions prone to seismic activity or for pipes subject to heavy traffic loads.
- Corrosion-resistant grades: Enhanced with additional alloying elements like copper, nickel, or chromium to improve corrosion resistance.
HOW TO CHOOSE THE RIGHT GRADE
Selecting the appropriate material grade for ductile iron pipes depends on various factors, including the type of fluid being transported, operating pressures, environmental conditions, and specific project requirements. Engineers must consider these factors in conjunction with the material properties to choose the most suitable grade that ensures the reliability, longevity, and performance of the piping system.
CORROSION OF DUCTILE IRON PIPES
Corrosion is a critical concern for ductile iron pipes, as it can significantly impact their longevity, functionality, and the quality of the water they transport. Understanding the mechanisms of corrosion, its effects, and strategies for mitigation is essential for maintaining the integrity of ductile iron pipe systems.
Mechanisms of Corrosion
- Galvanic Corrosion: Occurs when ductile iron is in contact with a more noble metal (e.g., copper) in the presence of an electrolyte, leading to accelerated corrosion of the iron.
- Pitting Corrosion: A localized form of corrosion that leads to the creation of small holes or pits on the pipe surface. This is often caused by the presence of chlorides and low pH levels in the water.
- Microbiologically Influenced Corrosion (MIC): Caused by certain bacteria that can produce corrosive by-products, leading to accelerated corrosion rates.
- Graphitic Corrosion: Involves the selective leaching of iron from the ductile iron, leaving behind a graphite matrix with little structural integrity.
Effects of Corrosion
- Reduced Pipe Life: Corrosion can significantly shorten the lifespan of ductile iron pipes, leading to premature failures and the need for replacements.
- Decreased Water Quality: Corrosion by-products can contaminate the water supply, affecting its taste, color, and safety.
- Increased Maintenance Costs: Corroded pipes may require more frequent repairs and maintenance, leading to higher operational costs.
Corrosion Mitigation Strategies
- Cathodic Protection: A method that involves attaching a sacrificial anode to the pipe or using an impressed current to protect the pipe from corrosion. This technique redirects the corrosive activity to the anode, which corrodes instead of the pipe.
- Coatings and Linings: Applying protective coatings externally and linings internally can shield the pipe from corrosive elements. Zinc coatings, for instance, provide galvanic protection, while epoxy or cement-mortar linings prevent direct contact between the water and the pipe interior.
- Control of Water Chemistry: Adjusting the pH levels and controlling the concentration of aggressive ions (such as chlorides) in the water can reduce corrosion rates.
- Corrosion Inhibitors: Adding corrosion inhibitors to the water can form a protective film on the pipe’s interior surface, slowing down the corrosion process.
- Design Considerations: Designing the piping system to minimize stagnant water areas, ensure proper drainage, and avoid direct contact with more noble metals can help reduce the risk of corrosion.
- Regular Monitoring and Maintenance: Implementing a regular inspection and maintenance program to detect early signs of corrosion and address them promptly.
LINING & COATING FOR DUCTILE IRON PIPES
Lining and coating are crucial protective measures for ductile iron pipes, extending their service life by preventing corrosion and ensuring the quality of the conveyed fluids. These treatments not only safeguard the pipe internally and externally against corrosive environments but also contribute to improved hydraulic performance and reduced maintenance costs. Here’s an overview of common linings and coatings used for ductile iron pipes:
Internal Linings
Cement-Mortar Lining
- Application: Widely used for potable water distribution due to its excellent protection against tuberculation (the buildup of mineral deposits) and its pH-neutral properties, which protect the pipe from aggressive waters.
- Benefits: Enhances flow characteristics, reduces energy costs, and minimizes bacterial growth.
Polyethylene (PE) Lining:
- Application: Suitable for pipes transporting aggressive chemicals, sewage, and wastewater.
- Benefits: Offers outstanding chemical resistance, preventing the pipe interior from chemical attack.
Epoxy Lining:
- Application: Used for both potable water and industrial applications where chemical resistance and smooth surface for improved flow are required.
- Benefits: Provides a durable, seamless, and corrosion-resistant barrier.
Polyurethane Lining:
- Application: Ideal for abrasive and highly corrosive environments, such as in mining operations and sewage applications.
- Benefits: Offers excellent abrasion resistance and longevity, even in harsh conditions.
External Coatings
Zinc Coating:
- Application: A standard protective coating applied to the exterior of ductile iron pipes, often topped with a finishing layer of bituminous paint or a polymeric topcoat for additional protection.
- Benefits: Acts as a sacrificial anode, corroding in place of the iron (galvanic protection) and significantly extending the pipe’s life.
Polyethylene Encasement:
- Application: Typically used in aggressive soil conditions. The pipe is encased in a loose polyethylene sleeve that acts as a barrier between the pipe and the surrounding soil.
- Benefits: Effective in preventing corrosion from soil aggressivity, with the additional advantage of being simple and inexpensive to apply.
Fusion-Bonded Epoxy Coating:
- Application: An external coating applied as a powder that melts and fuses to the pipe surface, used in both potable water and wastewater systems.
- Benefits: Offers excellent chemical resistance, durability, and protection against corrosion and UV degradation.
Polyurethane Coating:
- Application: Applied for external protection in highly corrosive environments and areas with high UV exposure.
- Benefits: Provides superior resistance to impact, abrasion, and chemical exposure, preserving the pipe’s integrity over time.