This article explains the main differences between “Forged” vs “Seamless” Pipes and why forged pipes may have advantages over standard seamless pipes in heavy-duty applications that require enhanced chemical and mechanical properties (for example: fluids conveyance within nuclear power plants) or in other, specific, circumnstances (small lots production, for instance).
FORGED Vs. SEAMLESS PIPE
WHAT IS A FORGED PIPE?
Definition
A forged pipe is a type of pipe created through the process of forging, which is a manufacturing technique that involves shaping metals through localized compressive forces. The term “forged” refers to the process by which the pipe is made and not to the shape or specific use of the pipe.
The forging process typically involves heating a piece of metal, and then hammering or pressing it to form the desired shape. For pipes, this process usually starts with a cylindrical “billet” of metal that is pierced to create a hollow center, much like the initial steps in seamless pipe manufacturing. The difference lies in the subsequent steps where the metal is mechanically worked to produce the final dimensions and properties.
Manufacturing Process of Forged Pipes
The key steps used to produce forged seamless pipes are depicted in the image below:
Billet Preparation
The process begins with the preparation of solid cylindrical billets made of steel or other suitable materials. These billets are typically produced through methods such as continuous casting or hot rolling and are cut to the desired length for further processing.
Billet’s Heating
The billets are heated to high temperatures in a controlled atmosphere furnace to make them more malleable and easier to deform. Heating is crucial for reducing the material’s yield strength and facilitating plastic deformation during the forging process.
Forging
The heated billets are placed under a forging hammer or press, where they undergo plastic deformation to shape them into the desired form of pipes. The forging process involves applying compressive forces to the billets to deform them into cylindrical shapes resembling pipes.
Forging may be performed in multiple stages to achieve the desired dimensions, shapes, and mechanical properties of the forged pipes.
Piercing
After forging, the rough forged blanks are pierced to create a hollow tube with a uniform inner diameter. Piercing involves forcing the forged blanks through a series of dies and rollers to remove excess material and form the inner surface of the pipes.
Rolling and Sizing
The pierced blanks are then elongated and reduced in diameter through a series of rolling passes to achieve the desired dimensions and wall thickness. Rolling and sizing processes may involve hot or cold rolling techniques, depending on the material properties and requirements of the forged pipes.
Heat Treatment
Once the pipes are formed and sized, they undergo heat treatment processes such as annealing or tempering to improve their mechanical properties and microstructure. Heat treatment helps to relieve internal stresses, refine the grain structure, and enhance the strength, toughness, and ductility of the forged pipes.
Machining
After heat treatment, the forged pipes undergo machining operations such as turning, boring, and threading to achieve the final dimensions, surface finish, and tolerances required for their intended applications. Machining helps to refine the surface finish, remove any surface defects, and ensure the dimensional accuracy of the forged pipes.
Testing and Inspection
Throughout the production process, forged pipes undergo rigorous testing and inspection to ensure quality and conformance to specifications. This may include non-destructive testing methods such as ultrasonic testing, eddy current testing, and visual inspection, as well as destructive testing methods such as tensile testing and hydrostatic testing.
Finishing and Packaging
Once the forged pipes have passed all quality checks and inspections, they are carefully finished, cleaned, and packaged for shipping to customers or distribution centers. Proper packaging helps to protect the pipes during transit and storage, ensuring they arrive in optimal condition.
In summary, the production process of forged pipes involves a combination of forging and machining techniques to create seamless pipes with enhanced mechanical properties and dimensional accuracy. By following stringent quality control measures and employing advanced manufacturing technologies, forged pipe manufacturers can deliver reliable and durable products that meet the demanding requirements of various industries and applications.
The picture below represents a forging press of approximately 12.000 tons:
Key Features of Forged Pipes
- Enhanced Strength: Forging refines the grain structure of the metal, aligning it to the shape of the pipe. This produces a uniformity of composition and structure, which grants superior strength and fatigue resistance compared to cast or machined parts.
- High Durability: The absence of seams in forged pipes means there are no weak points, making them highly durable and capable of withstanding extreme internal pressures and stressful environmental conditions.
- Customizability: Forged pipes can be tailored to specific sizes and shapes to meet unique requirements, a process that is more flexible than casting or extrusion.
- Superior Reliability: With a homogenous structure, forged pipes are more reliable for high-stress applications as they are less likely to contain hidden defects such as voids or inclusions that can lead to failure.
- Chemical Resistance: The lack of seams and the uniformity in structure also contribute to improved chemical resistance, as there are no paths of lesser resistance for chemicals to exploit.
- Thermal Stability: Forged pipes offer exceptional thermal stability, maintaining their structural integrity across a wide range of temperatures, which is essential for pipes used in high-temperature processes.
- Corrosion Resistance: With no welds or seams that can be prone to corrosion, forged pipes have an inherent advantage in corrosive environments over welded counterparts.
Elective Applications of Forged Pipes
- High-Pressure Applications: Forged pipes are well-suited for systems that operate under high internal pressures, such as hydraulic systems.
- Oil and Gas Industry: They are used in drilling and transport where strength and pressure resistance are paramount.
- Power Generation: Within power plants, especially in critical areas where failure could result in severe consequences.
- Chemical Processing: In the manufacturing of chemicals, where pipes need to withstand corrosive substances.
- Marine Applications: Where the combination of strength and corrosion resistance is essential due to the harsh marine environment.
- Nuclear Industry: Forged pipes are beneficial for their reliability and the ability to withstand the demanding conditions of nuclear plant operations.
WHAT IS A SEAMLESS PIPE?
A seamless pipe is a type of pipe without any welded joints or seams. It is a solid cylindrical steel pipe created by drawing a solid billet over a piercing rod to create a hollow shell.
Piercing mill seamless pipes
The production process of seamless pipes is fully automated and mainly oriented to standard sizes and large quantities (an order could go from a minimum quantity of 20 pipes to a pipeline order with 5.000 km / 450 pipes of the same size). Pipes are not mechanically CNC machined except for the ends (pipe ends are beveled or threaded to allow connection of each pipe).
The manufacturing process of a seamless pipe can be outlined as follows:
Heating of the Billet: A solid round steel billet is heated at a high temperature to make it pliable.
- Piercing: Once the billet is heated enough, it is pierced through the center using a piercer to create a hollow shell. This is often done on a rotary piercing mill where the billet is fed between rollers and a mandrel (piercing rod) to start the hollowing process.
- Rolling: The hollow shell is then elongated and rolled to give it the desired thickness and diameter. This is usually achieved using a series of rolling mills, which may include a mandrel mill and plug mill. In the mandrel mill, a mandrel bar is inserted into the tube and the assembly is then rolled until the desired dimensions are achieved.
- Sizing: After rolling, the tube may be further processed to achieve the precise size and tolerances required. This can include additional passes through a reducer mill and sizing mill.
- Heat Treatment: To achieve the desired mechanical properties, the pipe is then subjected to heat treatment such as annealing or quenching and tempering.
- Finishing: Finally, the pipe undergoes finishing steps, which may include cutting, straightening, inspecting, and sometimes further machining.
Learn more about seamless pipes and their manufacturing process.
Seamless pipes are widely used in applications where strength under extreme pressure is a necessity, such as in the oil and gas industry, chemical and power plants, and machinery parts. They offer a high level of integrity and are considered suitable for high-pressure, high-temperature, and harsh chemical environments because they can handle greater stress and are more durable than welded pipes, which have a seam that may be considered a weak point.
KEY DIFFERENCES FORGED VS. SEAMLESS
KEY DIMENSIONAL PARAMETERS
The size of a forged pipe is defined by:
- Outside diameter (OD)
- Inside Diameter (ID)
Forged pipes are also called “ID controlled” or “Minimum Wall Thickness Pipes” (as a minimum thickness is granted).
Instead, the size of a seamless pipe is defined by:
- Outside Diameter (OD)
- Wall Thickness (WT)
- Forged vs seamless pipe dimensions
Seamless pipes are also called “OD-controlled pipes” or “Average Wall Thickness Pipes”. The theoretical size of each pipe is different from the actual one (due to limitations in production, and the international norms allowing some dimensional tolerances). For example, in an OD-controlled size OD711 mm x WT 50 mm, the actual ID might show a 25 mm difference from the ordered (= theoretical) one.
This size difference (actual vs. theoretical) might generate unexpected costs and delays during installation at the site. This is due to the fact, for instance, that the welding of two pipes with different IDs might require longer time or extra machining of pipe ends (that were not accounted for during the pipework engineering process).
Imperfect welding might be very critical in offshore applications or for pipes installed within a power plant (as high-temperature steam might generate unwanted vortex movements, cavitation, and creep problems to all the ancillary utilities existing in the plant).
COST-EFFECTIVENESS
Theoretically, a forged pipe could be produced in any desired size. The question is: when is it better to go for a forged vs. a seamless pipe?
In general, forged pipes are more cost-efficient, compared to seamless pipes, in the following cases and applications:
- Larger OD (outside diameter): forged pipes show an overall cost advantage for larger OD pipes, say OD > 18” as a rule of thumb
- Heavier wall thickness pipes: forged pipes are the elective choice for applications that require heavy wall thickness pipes, for example from 40/50 mm WT upwards
- Special Dimensional Tolerance or Surface Finishing required by the project: due to its fine manufacturing process, forged pipes can be produced to custom dimensions and precise tolerances (whereas, as explained above, seamless pipes show a constant divergence between actual vs. theoretical sizes)
- Small production lots (because the minimum order size for a forged mill is just 1 pipe, whereas seamless pipes manufacturers have minimum lot quantities of several tons, generally above 10)
On the contrary, Seamless Pipes are more cost-efficient in the following cases:
- OD: standard sizes from 12,7 mm (1/2″) to 457 mm (18″)
- The project requires pipes with standard wall thickness, for example below 25/30 mm
- Large lots: minimum order is 200 meters / 20 pipes per size
The image below shows the competitive range for forged pipes (vs. seamless pipes) in terms of pipe OD (outside diameter) and WT (wall thickness):
- forged pipes competitive range
TYPICAL CASES OF APPLICATION
Forged seamless pipes find applications across a wide range of industries due to their superior strength, durability, and reliability. Some of the key fields of application for forged seamless pipes include:
Oil and Gas Industry
- Forged seamless pipes are extensively used in the oil and gas industry for exploration, production, transportation, and refining processes.
- They are employed in drilling operations, well completion, pipeline construction, and transmission of crude oil, natural gas, and refined petroleum products.
- These pipes withstand high-pressure, corrosive environments, and extreme temperatures encountered in upstream, midstream, and downstream operations.
Petrochemical and Chemical Industry
- Forged seamless pipes are crucial components in petrochemical and chemical plants for conveying various chemicals, acids, and corrosive fluids.
- They are used in reactors, heat exchangers, distillation columns, and other process equipment where resistance to chemical corrosion and high temperatures is essential.
Power Generation
- Forged seamless pipes play a vital role in power generation facilities such as thermal power plants, nuclear reactors, and renewable energy installations.
- They are utilized in boilers, steam turbines, condensers, and heat recovery systems for transporting steam, water, and other fluids at high temperatures and pressures.
Aerospace and Defense
- Forged seamless pipes are used in aerospace and defense applications for manufacturing aircraft components, missile systems, and military vehicles.
- They are employed in critical systems such as hydraulic systems, fuel lines, and structural components requiring lightweight yet strong materials with high fatigue resistance.
Mechanical and Automotive Engineering
- Forged seamless pipes find applications in mechanical engineering and automotive industries for manufacturing shafts, axles, gears, and other precision components.
- They are used in high-performance automotive exhaust systems, suspension components, and drivetrain assemblies requiring superior strength and durability.
Infrastructure and Construction
- Forged seamless pipes are used in infrastructure and construction projects for structural support, piling, and foundation works.
- They are employed in bridges, buildings, tunnels, and offshore structures for structural applications requiring high load-bearing capacity and resistance to corrosion and environmental factors.
Mining and Exploration
- Forged seamless pipes are utilized in mining and exploration activities for drilling, extraction, and transportation of minerals, ores, and fluids.
- They are employed in drilling rigs, wellbore casing, and pumping systems for mining operations and mineral processing plants.
Marine and Offshore
- Forged seamless pipes are employed in marine and offshore applications for offshore drilling, production platforms, and subsea pipelines.
- They withstand harsh marine environments, high pressures, and corrosive seawater conditions encountered in offshore oil and gas exploration and production.
ADVANTAGES OF FORGED VS. SEAMLESS PIPES
Forged pipes offer several advantages over seamless pipes, particularly in applications that demand high strength and reliability. Below are some scenarios where forged pipes are preferred over seamless pipes:
TECHNICAL REASONS
High-Pressure Tolerance
Forged pipes have superior strength and are preferred in high-pressure applications. The forging process increases the strength of the metal by aligning the grain according to the shape of the pipe, thereby making it more resistant to internal pressures.
Improved Mechanical Properties
Through forging, the metal’s mechanical properties are enhanced due to the refinement of its microstructure and the closure of porosity. This makes forged pipes ideal for heavy-duty applications where strength, ductility, and toughness are crucial.
Chemical Consistency
The forging process can result in a more homogeneous material that has consistent chemical properties throughout, making it reliable for sensitive processes such as those found in the chemical and nuclear industries.
Reduced Chance of Defects
Since forged pipes are made from a single piece of metal that has been shaped under high pressure without welding or seams, there is a reduced chance of defects such as inclusions, voids, or weak spots that could be points of failure under stress.
Durability in Fluctuating Conditions
Forged pipes typically exhibit excellent fatigue resistance and long-term durability, even in applications where the temperature or pressure may fluctuate significantly.
Custom Alloys
Forging allows the creation of pipes from alloys that might not be feasible with seamless pipe production methods, which can be essential for applications requiring material properties that are not available in standard pipes.
COMMERCIAL REASONS
Customization and Sizes
Forged pipes can be customized more readily to desired sizes and thicknesses, which can be particularly beneficial for bespoke applications where standard pipe sizes are not suitable.
Cost-Effectiveness for Small Quantities
For small batch sizes, forged pipes can be more cost-effective to produce than seamless pipes due to the less complex manufacturing process.
In applications where these attributes are critical, forged pipes are often the preferred choice over seamless pipes, providing a reliable and robust solution for industries like oil and gas, power generation, and nuclear energy.
SUMMING UP
Overall, forged seamless pipes are indispensable components in various industries and applications where high-performance piping solutions are required to withstand extreme conditions and ensure reliable operations.
As a general indication, heavy wall-thickness forged pipes are used in more demanding applications than conventional seamless pipes:
- Power Generation steam lines, for instance, require high chrome content (alloy grade 11, grade 22, grade 91, grade 92) and heavy wall thickness lines to resist the high temperatures generated by the energy production process.
- A controlled ID Diameter pipe allows better dimensioning during the engineering stage, reduces welding costs during pipe installation, and furthermore reduces vortex fluid movements & creep risks inside the piping of the plant.
- Offshore parts subject to High Mechanical Stress like Risers, J-Lay Collars, and Spool Pieces are supplied in X grades (X60/X70). Those parts require high mechanical properties, in particular very high tensile strength at low temperatures (for example: an expected crush with the offshore pipeline could create serious damage to the pipelines) and require very strict machining tolerances (for example: pipelines need to be clean with pigs on a routine basis).
- Another common application of forged pipes is for OCTG Couplings in Upstream applications (for example: couplings for OCTG casing pipes size 18 5/8”) for heavy dimensions & heavy thickness that cannot be produced by using the standard seamless production process.
Some examples of forged steel products for application in the oil & gas, power generation, and heavy manufacturing industries
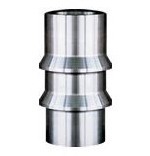
Forged J-Lay Collars
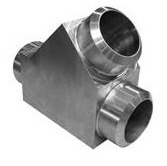
Forged Y-Pieces
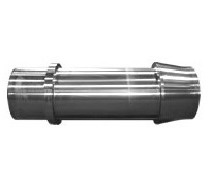
Forged Spool Pieces
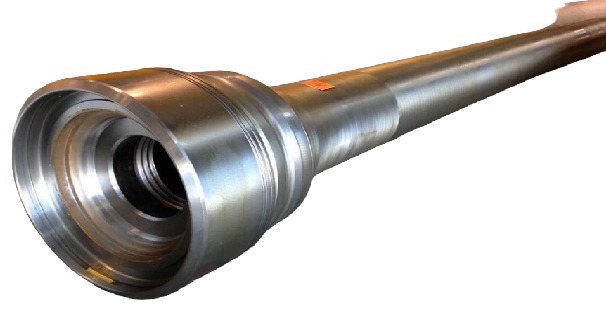
Forged Riser
KEY MANUFACTURERS OF FORGED PIPES
The market for forged pipes is a niche segment of the larger pipes market and is populated by a large number of small/medium-sized manufacturers.
The world’s most qualified forgings mills are located in Northern Italy (more than 20 suppliers) and Germany, along with some smaller production sites in China.
For Seamless Pipes, we have identified 2 categories of manufacturers (depending on the steel grade family):
- Carbon steel pipes: global supply is dominated by global groups such as Tenaris + Vallourec + Sumitomo, while Chinese manufacturers are playing a smaller role. Markets like the USA, Saudi Arabia, and Russia see a strong presence of local suppliers, with sales limited to their local markets
- Stainless Steel pipes: European manufacturers (Salzgitter DMV / Tubacex /Sandvik) are sharing the market with growing Chinese competition
Here is a list of global-scale manufacturers (multinational companies) known for producing forged steel pipes:
- Vallourec: Vallourec is a global leader in the production of seamless and welded steel tubes and pipes. They offer a wide range of forged steel pipes for various industries, including oil and gas, power generation, and petrochemicals.
- Tubos Reunidos: Tubos Reunidos is a Spanish manufacturer specializing in the production of seamless steel pipes, including forged pipes for the oil and gas industry, energy sector, and mechanical applications.
- Nippon Steel Corporation: Nippon Steel Corporation is a Japanese steelmaker known for its expertise in producing high-quality steel products, including forged pipes for offshore and onshore applications in the oil and gas industry.
- TMK Group: TMK Group is a leading global manufacturer of steel pipes, including seamless and welded pipes for various industries. They produce forged steel pipes for drilling, exploration, and production applications in the oil and gas sector.
- Tenaris: Tenaris is a multinational manufacturer of seamless and welded steel pipes and related services. They offer a wide range of forged steel pipes for use in critical applications such as oil and gas drilling, refining, and transportation.
- Borusan Mannesmann: Borusan Mannesmann is a Turkish manufacturer of seamless steel pipes, including forged pipes for energy, construction, automotive, and industrial applications.
- JFE Steel Corporation: JFE Steel Corporation is a Japanese steelmaker known for its production of high-quality steel products, including forged pipes for the oil and gas industry, mechanical engineering, and automotive applications.
- United States Steel Corporation (U.S. Steel): U.S. Steel is an American steel producer offering a variety of steel products, including forged pipes for energy, infrastructure, and construction applications.
- Sandvik AB: Sandvik AB is a Swedish multinational company specializing in high-performance materials and solutions, including forged steel pipes for demanding applications in the oil and gas, chemical, and aerospace industries.
- Ovako Group: Ovako Group is a European manufacturer of engineering steel products, including forged pipes for mechanical applications in the automotive, mining, and construction sectors.
It’s important to note that this list is not exhaustive, and there are many other manufacturers around the world producing forged steel pipes for various industries and applications. Additionally, the availability of specific products may vary depending on geographical location and market demand.
Please contact us in case you need recommendations based on steel grade, size, and pipe weight.
ASTM MATERIAL GRADES FORGED VS. SEAMLESS PIPES
The table below shows the most common material grades of seamless pipes and their forged equivalent:
MATERIAL TYPE | SMLS PIPE GRADE | FORGED GRADE | |
---|---|---|---|
CS - Carbon Steel - High Temperature | ASTM A106 gr B / A53 gr B / API 5L gr B/X42 PSL1 | ASTM A105 | |
CS - Carbon - Low Temperature | ASTM A 333 gr 6 | ASTM A350LF2 | |
CS - Carbon Steel | API 5L gr B / X42 PSL1 | ||
CS - Carbon Steel | API 5L gr B / X42 PSL2 | A694 F42 | |
CS - Carbon Steel | API 5L gr X42 PSL2 | ||
CS - Carbon Steel | API 5L gr X52 PSL1 | ||
CS - Carbon Steel | API 5L gr X52 PSL2 | ASTM A694 F52 | |
CS - Carbon Steel | API 5L gr X65 PSL1 | ||
CS - Carbon Steel | API 5L gr X65 PSL2 | A694 F65 | |
CS - Carbon Steel - Galvanized | ASTM A 53 gr. B | ASTM A105 | |
AS - Alloy | ASTM A 335 P11 | ASTM A182 F11 | |
AS - Alloy | ASTM A 335 P22 | ASTM A182 F22 | |
AS - Alloy | ASTM A 335 P5 | ASTM A182 F5 | |
AS - Alloy | ASTM A 335 P9 | ASTM A182 F9 | |
AS - Alloy | ASTM A 335 P91 | ASTM A182 F91 | |
SS - Stainless | ASTM A 312 TP304-304L | ASTM A182 F304-F304L | |
SS - Stainless | ASTM A 312 TP316-316L | ASTM A182 F316-F316L | |
SS - Stainless | ASTM A 312 TP321 | ASTM A182 F321 | |
SS - Duplex 22 | ASTM A790 UNS S31803 | ASTM A182 F51 | |
SS - Superduplex 25 | ASTM A790 UNS S32750 / 32760 | ASTM A182 F53 / F55 | |
SS - Inconel - Nichel Alloy 6625 | ASTM B444 UNS N06625 | ASTM B564 UNS N06625 | |
SS - Inconel - Nichel Alloy 8825 | ASTM B423 UNS N08825 | ASTM B564 UNS N08825 | |
CUNI - Cupronickel (CuNi 90/10) | ASTM B466 UNS C70600 | UNS C70600 | |
CUNI - Cupronickel (CuNi 70/30) | |||
Conclusion
In conclusion, forged steel pipes are indispensable components in numerous industries, providing reliable and durable solutions for transporting fluids, gases, and solids in demanding environments. From their robust manufacturing process to their diverse applications and inherent advantages, forged steel pipes continue to play a vital role in infrastructure development, industrial processes, and technological advancements worldwide. As industries evolve and demand for high-performance piping solutions grows, forged steel pipes remain at the forefront of innovation and excellence, ensuring the safe and efficient operation of critical systems across the globe.
13 Responses
I thankful for you sharing this important information. Also visit: Metalica Forging Inc is a market leader in Stainless Steel Flange Manufacturer in India.
Thank you for your appreciation and for sharing the link to Metalica Forging Inc. It’s great to see that you are a market leader in the field of stainless steel flange manufacturing in India. Your expertise in this area must be valuable to those seeking high-quality flanges.
In the context of the previous conversation about forged and seamless pipes, it’s interesting to note that both forged and seamless manufacturing processes are crucial in producing various components, including flanges. The article highlights the differences between forged and seamless pipes, such as the manufacturing process, sizes denominations, dimensional range, and applications.
Considering your expertise in manufacturing stainless steel flanges, it would be insightful to discuss how the manufacturing processes for pipes and flanges differ, and how these differences might impact the final product. Additionally, if you have any specific insights or experiences related to the topic of forged or seamless flanges, we would greatly appreciate your input.
Thank you again for sharing your knowledge and expertise on stainless steel flange manufacturing in India.
Hello, Very Informative article. It was nice to read the information you shared in the blog. Also if you are looking for Stainless Steel Round Bar Manufacturer in India do visit Girish Metal India.
Thank you for your kind words, Girish Metal India! We’re glad to hear that you found the article on forged vs. seamless pipes informative. It’s always great to provide valuable information to our readers.
We appreciate you sharing your link for Stainless Steel Round Bar Manufacturers in India. It’s important to have reliable sources when looking for specific products. We encourage our readers to explore different options and find the best manufacturers that suit their needs.
If you have any further insights or thoughts on the topic of forged vs. seamless pipes, we’d love to hear them. Thank you again for your contribution to the discussion!
Well written blog, we are certified Stainless Steel Pipe Manufacturer, Supplier in Kenya
Hi, Adorable Blog and this is something new I am reading on Blogger, we are DChel Weld We are leading,welding electrodes manufacturer in India, Welding electrodes manufacturer in Gujarat, Welding Electrode Manufacturer in Bangladesh, Welding Electrode Manufacturer in Bangalore
Hi, Adorable Blog and this is something new I am reading on Blogger, we are Sandco Metal Industries We are leading,stainless steel pipe manufacturers in ahmedabad,stainless steel pipe manufacturers in delhi,stainless steel pipe manufacturer in India,Stainless Steel Pipe Weight Chart,Stainless Steel Pipe Manufacturer in Saudi Arabia and Stainless Steel Pipe Manufacturer in Bhubaneswar</a
Nice info, Goyal Steel Tubes, the oldest dealer of MS Pipes and Tubes in Delhi-NCR, deals in all sizes and variety of MS Pipes, stocked from reputed companies like APL Apollo, Jindal, Surya etc.
Send your pipe related queries on 9650705448, call on 9910495448 or find us on google- Goyal Steel Tubes click on the first link.
Very detailed information providing specific details of each type of pipe.
Thanks for Sharing
Interesting, could you please add the names of the suppliers of forged pipes in Europe? We have been scouting for suppliers lately, without success. help appreciated, Mark
Dear Mark, please get in touch with us. We will send you the list of the forged steel pipes manufacturers in Italy (among the top world’s suppliers, both in terms of technical know how and cost effectiveness) and in Germany. Thank you for your interest in our article. Best, Projectmaterials
I think that this article is really very informative. You have explained the various applications of Stainless Steel Seamless Pipes and forged pipes in this article. You have also explained the materials and sizes in great detail. I have clearly understood the difference between these two types of pipes. Thank you very much for sharing this article with us.
Nice Information