Handling nitrogen safely in industrial plants is crucial due to its inert nature and the risks associated with its use, particularly in large quantities or under high pressure. Nitrogen is widely used for purposes such as creating inert atmospheres, as a blanketing gas, in cooling processes, and for purging equipment. Despite being non-toxic and inert, it can displace oxygen and create an asphyxiation hazard in confined spaces. In this article we take a look at the risks of Nitrogen in Oil & Gas plants and at the alternative ways to handle this critical substance safely.
NITROGEN (N2) IN OIL & GAS PLANTS
WHAT IS NITROGEN?
Nitrogen is a chemical element with the symbol N and atomic number 7. It is a colorless, odorless, tasteless, and mostly inert diatomic gas that constitutes 78% of the Earth’s atmosphere by volume, making it the most abundant uncombined element.

Nitrogen is a critical element in the biosphere and a fundamental building block of amino acids and nucleic acids, both essential components of all living organisms.
Nitrogen is a versatile and widely used gas in various industrial applications. Its unique properties make it an ideal choice for a range of processes, offering numerous benefits to industries across the board.
N2 PROPERTIES & BEHAVIOUR
Nitrogen is a nonmetal, placed in group 15 of the periodic table, commonly known as the pnictogens. It has five electrons in its outer shell and is trivalent in most compounds. The element exhibits a +3 or -3 oxidation state, although other oxidation states are also known.
At standard temperature and pressure, nitrogen is a gas, N₂, with a triple bond between the atoms making it exceptionally stable and inert. This stability is a key reason why nitrogen is unreactive in many situations. However, under specific conditions, nitrogen can form a vast array of compounds, including ammonia (NH₃), nitric acid (HNO₃), nitrates (NO₃⁻), and nitrites (NO₂⁻), which are vital for industrial applications and biological processes.
WIDE RANGE OF APPLICATIONS
Nitrogen has diverse applications across various industries:
- It is used in the production of fertilizers, where ammonia and nitrate-based compounds are critical for plant growth.
- In the chemical industry, nitrogen is used in the production of plastics, dyes, and explosives.
- The oil and gas industry uses nitrogen for inerting and as a blanket gas to prevent explosions.
- In the food industry, liquid nitrogen is used for freezing and preserving food, as well as in the cryogenic grinding of spices and other food materials.
- Additionally, nitrogen is used in the electronics industry during the production of transistors and diodes, and in metal processing and fabrication to prevent oxidation.
USE OF NITROGEN IN THE OIL & GAS INDUSTRY
Nitrogen plays a significant role in the oil and gas industry, offering a range of applications due to its inert properties, availability, and safety profile.
Its use spans from exploration and production to processing, transportation, and storage of hydrocarbons. Here’s a detailed look at the various applications of nitrogen in the oil and gas sector.
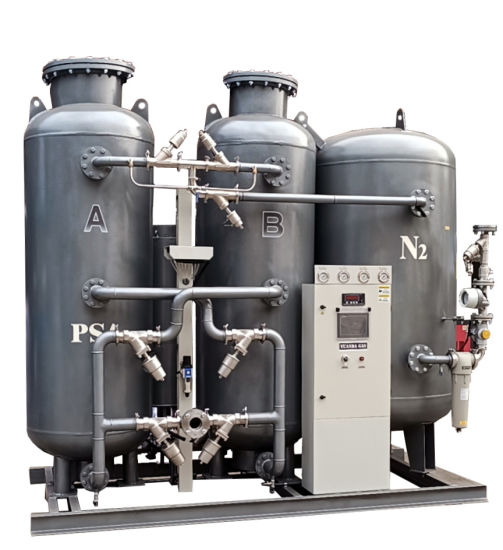
Enhanced Oil Recovery (EOR)
Nitrogen can be injected into oil reservoirs to increase reservoir pressure and significantly enhance oil recovery. This process, known as Nitrogen Enhanced Oil Recovery (N-EOR), involves injecting nitrogen gas to push additional oil towards the production wells. The injection of nitrogen helps maintain or increase the pressure in the reservoir, making it easier to extract the oil. This method is particularly useful in mature fields where natural reservoir pressure has declined.
Inerting and Purging
In the presence of oxygen, hydrocarbons can become highly explosive. Nitrogen is used to create inert atmospheres in tanks and vessels, preventing the ignition of flammable gases or liquids. Before maintenance or inspection activities, nitrogen purging is conducted to displace hydrocarbons and oxygen, minimizing the risk of explosion or fire. This application is critical for ensuring safety in refineries, pipelines, and during the transport of oil and gas products.
Gas Blanketing
Nitrogen gas blanketing is a process used to protect sensitive materials from air and moisture exposure. In the oil and gas industry, nitrogen blankets are used in storage tanks to prevent the oxidation of volatile organic compounds (VOCs) and to reduce vapor space above the liquid surface, minimizing the risk of explosion. This technique is essential for maintaining product quality and safety during storage and transport.
Leak Testing
Nitrogen is used for pressure testing and leak detection in pipelines, vessels, and other infrastructure. By pressurizing the system with nitrogen, operators can identify leaks through pressure decay tests or by using specialized detection equipment. This application is crucial for ensuring the integrity and safety of oil and gas infrastructure.
Well Stimulation
Nitrogen can be used for well-stimulation techniques such as nitrogen foam fracturing. This process involves injecting nitrogen under high pressure to create fractures in the reservoir rock, increasing its permeability and enhancing the flow of oil or gas. Nitrogen foam helps reduce the amount of water required for the fracturing process, minimizing environmental impact and improving well performance.
Drilling Operations
In drilling operations, nitrogen can be used to create foam-based drilling muds or as part of underbalanced drilling practices. Nitrogen foam drilling muds help reduce formation damage by minimizing the invasion of drilling fluids into the porous rock. Underbalanced drilling with nitrogen reduces the risk of differential sticking and formation damage, improving drilling efficiency and well productivity.
Safety and Maintenance
Due to its inert nature, nitrogen is widely used for safety and maintenance operations. It helps to extinguish fires in emergency situations and is used as a breathing apparatus for rescue operations in hazardous environments. Additionally, nitrogen purging and blanketing techniques are essential maintenance procedures to ensure the safety of equipment and personnel.
In conclusion, nitrogen is indispensable in the oil and gas industry due to its versatility, safety, and inert properties. Its applications range from enhancing oil recovery to ensuring the safety of operations, making it a vital component in the exploration, production, processing, and transportation of hydrocarbons. As the industry continues to evolve, the use of nitrogen is likely to expand, driven by ongoing efforts to improve efficiency, safety, and environmental sustainability.
SAFETY & N2 RISKS MITIGATION
Risk mitigation when using nitrogen in oil & gas plants is crucial to ensure the safety of personnel, protect the environment, and prevent damage to infrastructure. Implementing comprehensive risk management strategies involves identifying potential hazards, assessing the risks, and applying control measures. Here’s an overview of effective risk mitigation strategies for managing nitrogen use in oil and gas facilities:
TRAINING & AWARENESS VIA TRAINING
- Regular Training: Conduct regular safety training sessions for all personnel on the hazards associated with nitrogen use, including the risks of asphyxiation, cold burns, and over-pressurization. Training should also cover the correct use of personal protective equipment (PPE) and emergency response procedures.
- Awareness Campaigns: Implement awareness campaigns within the facility to keep safety considerations top of mind for employees, including signage and reminders about the dangers of nitrogen in areas where it is used or stored.
USE OF PERSONAL PROTECTIVE EQUIPMENT
- Appropriate PPE: Ensure that workers handling nitrogen, especially in its liquid form, are equipped with the appropriate PPE, including gloves, face shields, and safety glasses to protect against cold burns and frostbite.
- Oxygen Monitoring Devices: Equip personnel with portable oxygen monitoring devices in areas where nitrogen is used extensively to alert them to potentially dangerous reductions in oxygen levels.
ENGINEERING VERIFICATION
- Ventilation Systems: Install and maintain effective ventilation systems in areas where nitrogen is used or stored to prevent the buildup of an oxygen-deficient atmosphere.
- Leak Detection Systems: Implement leak detection systems for nitrogen storage and handling systems to quickly identify and address leaks.
- Pressure Relief Devices: Equip nitrogen storage vessels and systems with pressure relief devices to prevent over-pressurization and potential explosions.
SAFE HANDLING PROCEDURES
- Standard Operating Procedures (SOPs): Develop and enforce SOPs for the safe handling, storage, and use of nitrogen. Procedures should include steps for safe purging, blanketing, and injection operations.
- Emergency Response Plans: Establish clear emergency response plans for nitrogen-related incidents, including procedures for evacuation, first aid, and emergency medical treatment for exposure to low-oxygen environments or cold burns.
MONITORING & REGULAR INSPECTIONS
- Regular Inspections: Conduct regular inspections and maintenance of nitrogen handling and storage equipment to ensure they are in good working condition and free from leaks.
- Oxygen Level Monitoring: Continuously monitor oxygen levels in confined spaces and areas where nitrogen is used to ensure a safe working environment.
ENVIRONMENTAL PROTECTIVE MEASURES
- Minimize Releases: Implement measures to minimize accidental releases of nitrogen into the atmosphere, including using capture and recovery systems during venting operations.
- Environmental Impact Assessments: Conduct environmental impact assessments for large-scale nitrogen use projects to understand and mitigate potential impacts on the environment.
COMMUNICATION
- Clear Communication Channels: Establish clear communication channels and protocols for reporting safety concerns, incidents, and near-misses related to nitrogen use.
- Coordination with Emergency Services: Coordinate with local emergency services to ensure they are aware of the potential hazards associated with the facility and are prepared to respond to nitrogen-related incidents.
PROPER STORAGE AND TRANSPORTATION
Nitrogen must be handled with care to avoid accidents, including asphyxiation, explosions, and cold burns. Here’s a comprehensive guide on the best practices for the storage and transportation of nitrogen:
Appropriate Storage
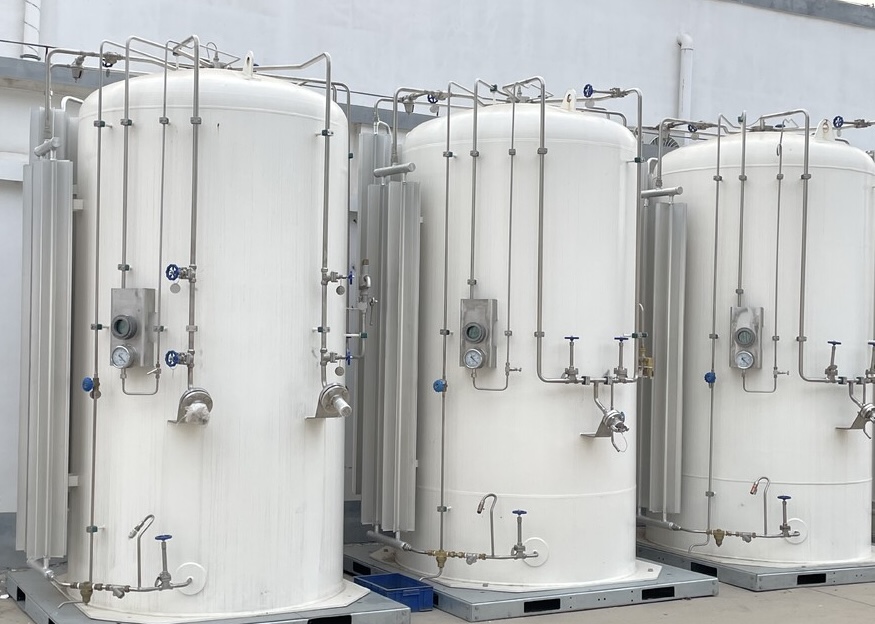
Gas Storage
- Cylinders and Tanks: Nitrogen gas is stored in high-pressure cylinders or gas tanks. These containers must be designed, manufactured, and maintained according to national and international standards to withstand the pressures involved.
- Labeling and Marking: All containers should be clearly labeled with the contents and the associated hazards. Safety signs should indicate that the area contains nitrogen, an asphyxiant gas.
- Secure Storage: Cylinders should be stored upright and secured to prevent them from falling over. Storage areas should be well-ventilated, away from direct sunlight, and in locations with stable temperature conditions.
- Distance from Combustibles: Ensure that nitrogen cylinders are stored away from flammable materials, sources of heat, and direct sunlight to minimize the risk of fire or explosion.
Liquid Storage
- Cryogenic Tanks: Liquid nitrogen is stored in cryogenic tanks, which are specially designed to maintain the extremely low temperatures required to keep nitrogen in its liquid state.
- Pressure Relief Valves: Cryogenic storage tanks must be equipped with pressure relief devices to prevent over-pressurization due to the expansion of liquid nitrogen.
- Insulation: Tanks should be well-insulated to minimize heat transfer and reduce the rate of nitrogen evaporation.
- Safety Space: A safety space (ullage) must be maintained within the tank to allow for expansion as liquid nitrogen absorbs heat.
Proper Transportation of Nitrogen
Gas Transportation
- Cylinder Transport: When transporting nitrogen gas cylinders, ensure they are properly secured in a vertical position, and the vehicle is well-ventilated. Use cylinder caps to protect the valves from damage.
- Regulations Compliance: Follow all relevant regulations and guidelines for the transportation of compressed gases. This includes proper vehicle labeling, placarding, and carrying the appropriate safety data sheets (SDS).
Liquid Transportation
- Cryogenic Liquid Tankers: Liquid nitrogen should be transported in specialized cryogenic liquid tankers equipped with insulation and pressure relief devices.
- Securing Tanks: Ensure that cryogenic tanks are securely fastened to the transport vehicle to prevent movement that could lead to spills or accidents.
- Temperature and Pressure Monitoring: Vehicles equipped with cryogenic tanks should have systems in place to monitor the temperature and pressure of the liquid nitrogen during transport.
Implementing a comprehensive risk mitigation strategy for nitrogen use in oil & gas plants involves a multifaceted approach that includes safety training, the use of PPE, engineering controls, standard operational procedures, regular monitoring and maintenance, environmental protection measures, and effective communication and coordination. By addressing the potential hazards associated with nitrogen proactively, facilities can significantly reduce the risks to personnel, operations, and the environment.